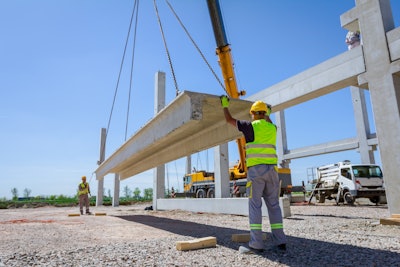
Injuries on jobsites aren’t just a result of major accidents. Oftentimes, they’re a gradual problem caused by poor ergonomics.
Common conditions like strains and sprains, tendonitis, carpal tunnel syndrome, and other musculoskeletal disorders (MSDs) are some of the leading causes of workplace injuries. The physical demands of construction work can take a toll on the body—putting your team at risk.
As a business owner, it’s up to you to make sure your employees are protected on all fronts. Taking minor precautions throughout the day can help reduce the risk of ergonomic issues.
Teach Proper Techniques
As with any safety issue, preparedness is a key. Training workers to understand proper ergonomics can help reduce the risk of injuries. Here are techniques you should be conscious of when it comes to ergonomics issues on your jobsites:
Lifting Objects
Few days go by on a project where workers don’t manually lift materials. Any object from lumber and steel parts to bricks and other bulky materials can cause injury when lifted improperly. Keep the following tips in mind if your team needs to lift an object:
- Use correct posture, like lifting with your legs, keeping your back straight, and avoiding twisting and bending over
- Consider the weight and configuration of an object before lifting
- Two people should lift and object that’s more than 60 pounds, awkwardly shaped, or oversized
- Break the load up into smaller parts if possible
- Use equipment to lift heavy objects when possible
Using Tools
While many tools can help reduce strain on the body during construction tasks, it's important to remember that even these tools require proper technique and awareness to minimize ergonomic risks.
- Limit excessive vibrations from devices such as impact drills, jackhammers, industrial grinders, and sanders. High amounts of vibration can cause a condition known as hand-arm vibration syndrome (HAVS). Due to the disruption of natural oxygen flow, vibrations can also cause issues like back pain and carpal tunnel syndrome.
- Use the correct tools for the task. While powered tools require less exertion, their weight can lead to other ergonomic issues
- Keep up with tool maintenance, like sharpening knives and drill bits, to help avoid additional exertion
- Use tools that are ergonomically designed, avoid handles that end in the middle of your palm
- Change positions, use padding, and switch hands periodically to help reduce pressure on your palms, wrists, and elbows
- Reduce torque and rotational force by using electric, pulse, or auto-shutoff tools
- Take breaks, change tasks frequently, and avoid repetitive tasks
- Avoid prolonged awkward postures and adjust your body position to get as close to the work as possible.
Proper Stretching
The tips above should provide general guidance for completing manual work. But what about before your team starts a task?
Take a few minutes before and after a shift to stretch, focusing on muscle flexibility and range of motion. The types of stretches may vary by task, but remember to:
- Relax and breathe normally
- Use gentle, controlled motions
- Keep your knees slightly bent for better balance
- Stretch until you feel mild tension, hold for about 15 seconds, then relax
- Focus on how you feel, not on how far you can stretch
Lean Into Your Workers’ Compensation Plan
Even if workers are careful, injuries can happen. That’s why it’s important to have insurance that can help protect your workers. Most states require businesses to have worker’s compensation coverage, but simply having a policy isn’t enough.
When you purchase insurance, you can also benefit from the safety services and claims support they offer. Make the most of it. Ask your insurer how they can help you reduce workplace and ergonomic risks. Or, if an injury occurs, how they can help your injured workers receive proper care—helping them return to work sooner and lowering overall costs.
For example, my safety team’s role is to help construction businesses with on-site risk assessments and safety trainings. Ergonomics and material handling are often a few of the training topics we assist with. Lean into the resources and support available to you. Improving workplace safety takes a collective effort, and your insurer can help.
Create a Return-to-Work Program to Support Injured Workers
Having a safety and insurance plan is a good first step. However, it’s also important to have a post-injury management plan to care for your injured workers. Streamline communication by assigning a team or manager in charge of workers’ compensation claims. That way, when an injury occurs, it can be reported quickly to the right people.
Your team’s response and timing can be critical. Missing details or a lag in reporting can lead to delayed benefits and access to support. Once a claim is submitted, remember to engage with your injured employees throughout their recovery. An injury not only affects the physical health of your employees—it can also impact their overall well-being. They need your support and reassurance.
One way to show your support is by developing a formal return-to-work program that welcomes your injured employee back. This should include meaningful job tasks that account for their physical restrictions. By finding light duty tasks and welcoming your employees back to work, you show your care, support, and commitment to their safety.
The Bottom Line
Ergonomic injuries are largely preventable. Help your team recognize tasks that may create physical limitations and use the resources available to put them in safer positions. The tips I’ve shared here can help you get started, but it’s best to talk with your team and local experts to create an ergonomics program specific to your projects and business. Just a few small steps can make a big difference when it comes to the safety of your employees.