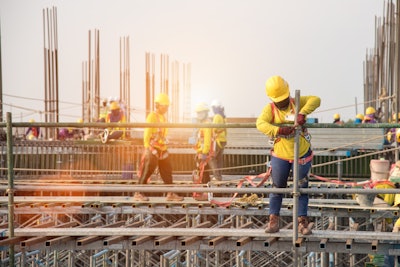
As industries evolve, the demand for specialized skills surpasses the available talent pool. To fill this need, many companies are turning to contractors and subcontractors. In fact, companies outsource 60-70% of contracted work to subcontractors. Since 2019, the ratio of contractors to employees has risen by 63% in the average company. Contract labor provides flexibility and cost savings. But it also presents its own set of challenges. As the use of contractors rose, fatal work injuries also grew 5.7% in the last year, with a worker dying every 96 minutes.
Contractors are often involved in these incidents. That’s why it’s critical to understand the risk associated with contract labor. Below, we will break down the biggest myths about contractor risk management.
Myth 1: Contractor and subcontractor risk management is not my problem.
Historically, we have seen a very contractual approach to managing contractors. In this traditional approach, businesses keep contract workers at arm’s length. They believe the contractor is at fault if something goes wrong.
This approach to managing contractors often leads to misalignments, such as how contractors manage their workforce, the quality of employees they bring to a job site, whether they subcontract the work, or, worse, compromises in workplace safety. The greater the misalignment between a business and a contractor, the greater the risk.
The truth is, if it’s your business contracting work, you are responsible for managing the associated risk—throughout your entire supply chain. Even small amounts of contracted work can have a catastrophic impact on a business. The easiest way to think of it is: whose name would be in the headline if something goes wrong?
As contract work continues to rise, businesses must be aware of the risks posed by contractors and subcontractors. Business leaders must intentionally create processes and establish safety protocols that align with their company’s values and the law. Then, you must communicate those throughout your entire supply chain. This includes everyone from employees to contractors and subcontractors. You should also evaluate these processes and protocols to ensure they align with modern safety practices.
Myth busted: Contractor and subcontractor risk management is your responsibility.
Myth #2: Compliant Companies have compliant and safe workers.
OSHA in the United States and HSE in the UK created parameters to reduce workplace injuries. Yet incidents like children dying in poultry plants or workers dying in trench collapses continue to occur. Company compliance is a good start, but it has limitations and does not guarantee incident-free work. In today’s economy, we need more than a corporate checklist for true compliance. We must ensure that the work is done safely — at the individual worker level. Reducing workplace injuries and fatalities lowers a business’s risk profile. It can also prevent potential fines or reputational damage.
The most progressive businesses manage individual worker compliance and set expectations for safety requirements at their site. For example, if you’re doing hot work, you need a current welder’s license; if you’re dealing with electricity, you need an electrician’s license. If you haven’t taken the on-site safety training, you aren’t allowed on-site until you do. These expectations allow businesses to move risk management from the company-level to the individual to run more efficient operations with fewer accidents.
Myth busted: Company compliance alone doesn’t guarantee worker safety.
Myth 3: Managing risk in silos creates more risk.
Oftentimes, in the case of a serious injury or fatality, an investigation shows leading indicators or data that could have helped prevent an accident. Unfortunately, due to siloes within the business and departments not communicating, these signs are easily missed.
It’s not uncommon for businesses to have repositories of knowledge spread across different business functions. In the case of contracted work, someone in the safety department will have different knowledge than someone in the insurance or procurement departments of the business. As a result, they may rely on each other to gain a full perspective of a contractor’s task and the risks associated. Any misalignment between these business functions or even between a business and its contractors could result in an accident.
So, how can an organization reduce these siloes? It starts at the top with line-of-business leaders and must be woven throughout the organization. Eliminating siloes doesn’t necessarily require every employee to know everything about every business function. Rather, it requires an alignment between line-of-business leaders, who agree to a process for connecting knowledge and relevant data across business functions. This will help build a baseline for risk awareness, increase trust, and ultimately, ensure safety as a result.
Myth confirmed: Managing many risk types in silos does create more risk.
Myth 4: AI can help in the future with safety and risk management, but not today.
Technology has improved the safety and risk management industry. It allows us to better manage risk at the speed of business. The same could be said for AI. Even as global AI spending is expected to surpass $300B by 2026, some organizations may be apprehensive about more broadly integrating AI into their risk management strategy, largely because questions remain about the risks associated with data privacy and AI.
Without adding much complexity or time, AI can function as a worker’s copilot, helping them identify contractor risks, implement controls, and safely complete a job. In fact, AI is likely working in the background at your current job site, running tasks like document verification or insurance verification.
While AI can’t replace the human touch of an ESG auditor or safety professional, it can augment their role by automating contractor risk management tasks. Most importantly, it can help businesses scale their risk mitigation and reduce incidents, injuries, and fatalities.
Myth busted: AI can help solve some of today’s most complex risk management problems.
Historically, risk and safety professionals have followed Heinrich’s triangle, assuming fewer incidents mean less severity. The problem? Severe risk isn’t limited to the triangle’s top. Risk is plausible from your largest suppliers and contractors. It is also plausible with your smallest suppliers and contractors. To reduce contractor risk across their supply chain, businesses can turn to technology to reduce siloes, ensure the right controls and practices are in place, and overall minimize the number of workplace injuries and fatalities.