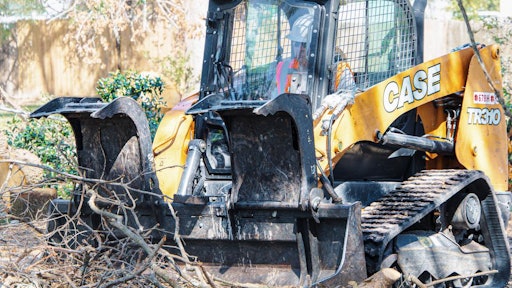
June begins the Atlantic hurricane season, which runs through November 30. Natural disasters present challenges for construction equipment and operators in such a way that calls for planning and preparation (tips can be found in “4 Natural Disaster Preparedness Tips for Construction Contractors” on ForConstructionPros.com).
Disaster Preparedness for Equipment
Disaster response has an immediate mobilization timeline, so a fleet must be ready to respond to the affected area as quickly as possible, noted Tyler Havens, Stellar Industries product manager.
Case in point: Team Rubicon (TR) is a veteran-led humanitarian organization serving global communities before, during and after disasters and crises. Its primary scope in heavy equipment disaster response includes route clearance, debris management and sawyer support.
“Our primary uses for the equipment are for route clearance, debris removal and vegetative debris removal,” said Jeremy Moore, TR operations manager. “We typically use the equipment in concert with our chainsaw crews to move the larger and heavier tree debris. Typically, we use [the] CASE TR310A/B for our heavy equipment needs.”
Fleet Management
Before a natural disaster strikes, ensuring that the right equipment is in a fleet and ready to perform vital tasks is a top priority, Havens said.
Construction companies should perform routine maintenance and machine upkeep to ensure that fleets are fully prepared to support disaster clean-up.Stellar Industries
During a natural disaster, proper disaster preparedness for equipment will ensure that necessary repairs can be conducted at the point of need during the response, reducing the likelihood of major breakdowns and subsequent disruption, said Havens.
“Sourcing items from local vendors will take more time in the recovery phase, so it’s essential to plan … and stock extra supplies,” he added.
When monitoring natural disaster seasons, such as the hurricane season, “knowing [the] typical areas that are hit the most and having a position where your equipment is in those areas is a critical step towards being ready,” said Ted Polzer, CASE North America director, product, and customer support.
Also, have solid tires to prevent flats leading to downtime because of sharp objects and debris on the ground, he said.
According to Justin Steger, John Deere product marketing manager, John Deere recommends that, for fleet management in known disasters, operators should plan and know how much fuel and diesel exhaust fluid are available and where they are located. Stock up on lubricants, grease and other needed fluids and parts, added Matt Costello, John Deere product marketing manager. Greasing machines will often play a significant role in keeping them operating especially if an operator is working in wet conditions, noted Costello, adding that it helps keep the joints clear and moving freely.
If equipment is in an area prone to natural disasters, identify special machine attachments, such as grapples, mulchers and forks, that can assist with cleanup.Caterpillar
Polzer said having a fuel supply in the event of a natural disaster is important, adding that, in some areas, “fuel can be a challenge to get because the roads are either treacherous or they're jammed.”
Contractors using electric equipment should consider having a good generator and accompanying supplies, said Polzer.
“It goes back to having your own power source and not depending on anyone else,” he said. “That way, you can control your own destiny.”
“If equipment is not used daily or weekly, make sure everything works as designed,” said Mayfield. “Not only do you want to make sure [that] the machine is ready to go, but the method of transportation is as well. Ensure [that] the trailer/truck is ready and that you have the proper tie-down equipment to secure the machine.”
Construction companies should perform routine maintenance and machine upkeep to ensure that fleets are fully prepared to support disaster clean-up, noted Steger.
“All machines should be properly greased; any underlying maintenance should be performed, and all issues should be fixed ahead of time, especially before forecasted hurricanes or snowstorms,” he said.
If the contracting company and its equipment are in an area prone to natural disasters, identify special machine attachments such as grapples, mulchers and forks that will assist in disaster recovery, Mayfield noted. Grapple attachments are best to have on hand for gripping fallen trees, debris and other items needing to be loaded and moved, Polzer said.
Grapples, brushes and mulching heads may prove effective in clean-up.John Deere
Costello said that brushes and mulching heads may prove effective in clean up.
“You can mulch up overburden like trees and branches,” Polzer said. “That might be a good investment because then you're not having to haul away wood chips and other debris, especially on roads that might be covered with debris, trees and powerlines. It makes it … difficult. You want to be as self-sufficient as you can be.”
If contractors don’t own the recommended attachments, they should rent attachments ahead of time for a machine, Mayfield said.
Polzer said he tells people to prepare themselves with the right equipment, “because what's also going to happen locally is that everybody in need of those attachments or tires is going to already be seeking them out, which drives up the price.”
It can be harder to get in the lead times because tires may have to be shipped from a greater distance “because somebody's already beaten them to the punch,” he added.
Fuel trailers and mechanic trucks are essential pieces of equipment that can help businesses and communities affected by natural disasters with clean-up, equipment repairs and refueling needs, said Havens. He added that they should be ready at a moment’s notice.
Taking care of the equipment that takes care of everything else can sometimes be overlooked. Regular maintenance is crucial to ensuring a work truck is prepared at all times.Stellar Industries
“A simple daily walk-around can identify and address potential issues before they escalate, providing the reassurance [that] a truck is operating at its full potential at all times,” he added.
To be prepared for natural disasters, TR volunteers perform monthly and quarterly maintenance.
“During these quarterly maintenance events, we ensure [that] we operate the equipment for 15 minutes to 30 minutes,” said Moore.
In situations such as wildfires, Polzer advises to follow firefighters’ guidelines to have the right protection gear in kits if a contractor is stranded.
“There’s a lot of good government guidance programs out there to support and drive an initiative to put in more firebreaks to try to reduce some of the risk,” Polzer said.
“Winch Optimization on New Fire Dozer Packages” on ForConstructionPros.com illustrates how winch optimization on new fire dozer packages developed based on input from the U.S. Bureau of Land Management, U.S. Fish and Wildlife Service, U.S. Forest Service, the Georgia Forestry Commission, and CAL FIRE for the Caterpillar D5 and its predecessor, the D6N. This optimization helps address the effort to save human lives, property and timber.
Dust and debris are often significant in areas affected by a natural disaster, noted Havens, adding that, after disaster strikes, inspecting the equipment exterior and tires for any punctures, wear or damage is important.
Fuel trailers and mechanic trucks can help businesses and communities affected by natural disasters with clean-up, equipment repairs and refueling needs.Stellar Industries
Before disaster strikes, “be mindful of where equipment is parked [because] potential falling hazards could damage equipment,” Steger said. “Additionally, move equipment to higher ground in instances of major flooding.”
Mayfield noted that machines moved away from the disaster area or to higher ground before disaster strikes should be secured to a trailer to be ready at a moment’s notice.
“Make sure you have all the proper personal protective equipment such as a hard hat, safety vests, steel-toe boots, communication tools, water and food ready to go,” he added.
“I can tell you from living in Kansas with tornadoes that, typically, we always used to park our equipment in low places—areas that had indentions in the ground,” Polzer noted. “Even though it would be full of debris, it wouldn't take direct shots from high-speed debris.”
Polzer said he’s seen contractors stage equipment just outside of an area that they believe will be hit.
“It won’t take that frontline type of wind gusts and damage because they're just outside that area,” he added. “A lot of contractors will have fleets of machines already loaded on trucks and trailers and ready. As soon as they're cleared to be able to start coming in to respond, they’re immediately in action.”
Contractors are encouraged to think of what other possible uses machines can have for cleanup or relief efforts, he added.
Before a predicted natural disaster occurs, operators should ensure that all cab doors and windows are closed before leaving the jobsite.John Deere
In a route clearance role, TR will stage equipment outside the projected path of the storm but close enough to quickly respond, noted Patrick Wright, Sr., TR heavy equipment associate.
Fleet Management During Natural Disasters
When operating in a disaster environment, it is paramount that detailed site surveys are conducted to identify existing and potential hazards, said Wright.
“Each piece of equipment requires both an operator and a spotter,” said Wright. “Spotters provide additional site awareness, operating assistance and crowd control. Pre- and post-operational inspections are conducted daily to identify equipment issues and provide preventive maintenance.”
Before a predicted natural disaster occurs, operators should ensure that all cab doors and windows are closed before leaving the jobsite, Steger said.
If a machine has vandal covers, they should be installed beforehand, if possible, to help save cab glass from damage from falling objects or debris, Steger said, adding that operators should also consider covering exhaust stacks to avoid unnecessary damage.
Costello noted that, when possible, a quick machine wash is helpful following a natural disaster to protect the machine’s components.
Operator Concerns
“Truck Manufacturers Pivot Designs, Embrace Change in Face of Natural Disasters, COVID 19” on ForConstructionPros.com illustrates how the challenges of natural disasters, the COVID 19 pandemic, supply chain and labor shortages amplified the importance of increased cab comfort for operators and how safety and technology updates serve to recruit and retain drivers.
Still, there are evergreen considerations. Operators should also be conscious of underfoot conditions as well as any compromised structures or fall hazards surrounding where they’ll be working, Steger said.
Other concerns include downed powerlines and natural gas leaks, Mayfield said.
Construction companies should perform routine maintenance and machine upkeep to ensure that fleets are fully prepared to support disaster clean-up.Stellar Industries
Operators should prioritize rest and hydration “just so they have their wits about them,” Polzer said. “Typically, they’re in an area that also has been hit. They’re already tired. They’ve got their own family on their minds.”
Proficiency is the largest operator concern, said Wright.
“Heavy equipment operation is a perishable skill and as a volunteer organization our challenge is to stay current on our skills and operational responsibilities,” he added.
“Operators must recognize that operating in a disaster zone is very different than in a controlled construction environment,” Wright noted. “Conditions and hazards are constantly changing. Many responders are not familiar with working around heavy equipment. Clear communication, safety briefs and site vigilance are paramount.”
Wright points out the volunteers spend many hours in the seat when deployed.
“Self-awareness and self-care are extremely important,” he noted. “Having two operators alternating throughout the operational period decreases fatigue and increases risk management effectiveness.”
Mayfield concurs that it’s important to be trained on each piece of equipment, whether it be for normal duty or in a natural disaster recovery situation.
Caterpillar’s Equipment Training Solutions offers e-learning modules and instructor-led programs for operators.
Also, many CASE contractors specialize in demolition.
“They’re used to looking for buried utilities in certain places, power lines and gas leaks. Not everyone has that experience level. That’s where you have to be aware of and understand exactly what those dangers are,” Polzer said.
“We’ve seen that in the Midwest, where a big tornado comes through and inexperienced operators might be in a heavy piece of machinery on a wooden floor going over a basement,” Polzer added. “A typical demolition person is accustomed to understanding that can be a problem.”
Protecting Equipment Post-Disaster
Following a disaster in which flooding is an issue, “depending on the extent of the flooding, you may need to change oils in the [different] compartments, such as axles and the transmission if it was submerged,” said Mayfield of fleet management during natural disasters. “Grease the machine more frequently when operating in water as well.”
Because machines will likely be used for tasks such as pulling trees, and moving debris, “as an operator, make sure you work within your experience level and think through recovery efforts as there are always safety issues present that you may not see,” Mayfield advises. “Ensure [that] no downed powerlines are active in the area where you are working.”
“If you're operating your machine in water over half of the track or the tire height right where there's water out to the axles or the drive train components, there’s an opportunity for the machine to take on water within the hydraulic system, which can create a lot of expense and downtime because of a failure,” said Polzer. He added that there needs to be a change in the typical maintenance pattern to an increased frequency.
Inspection procedures in a situation where there is a lot of debris call for looking for hoses that are chafed or fresh fluid leaks because debris fell on some hoses or tugged on them.
TR long-term recovery includes structure demolition with compact track loaders and excavators.
For those contractors who toggle between a regular project and helping in post-disaster cleanup, Polzer noted that one CASE client who focuses on road and bridge projects with their newer machines. Rather than trading in older machines, they keep them as backups for jobs such as post-disaster clean-up.
“As long as they have enough labor on the site, it doesn't really slow down their other projects,” he said. “If this is their only equipment and they are on a road and bridge project, they do need to consider if they don’t have solid tires, grapples and things like that if they are going to be less productive in that environment than other contractors equipped differently.
“You have to be prepared that you won't be as efficient and it’s possibly a challenge to get your equipment out. Clean-ups take longer than ever anticipated. It’s hard to forecast exactly what the commitment might be.”