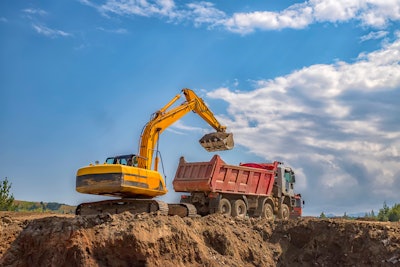
It would be great to complete every construction project exactly as you planned. With so many activities and things that can go wrong and out of your control, this would be nearly impossible. Building a perfect project would deliver the following performance:
- On-budget completion including crew field production.
- On-schedule completion with timely close-out.
- All contract requirements, targets, and goals met.
- Safe with no accidents.
- Quality workmanship without callbacks or punch list items.
- Proper documentation and communication without conflicts, issues, or disputes.
- Prompt and complete payment.
- A satisfied customer who provides excellent performance ratings and referrals.
To accomplish this standard, everything would have to go perfectly as planned. But you know this isn’t a reality in the ever-changing construction world. There are too many variables and things that can and will go wrong on every job. Potential problems range from material deliveries to the weather, from complete and accurate plans to crew workloads, and from field conflicts to getting paid. In fact, construction is one of the most difficult processes to monitor, manage, and control as there are just too many variables contractors can’t control.
Systems and Strategies Improve Project Results
How can you improve your construction project performance and eliminate potential issues that occur on your projects? Successful construction companies work hard and enforce standardized systems and controls to lower risk factors, eliminate potential problems, reduce the chances for things to go wrong, and improve their odds of achieving results. Some examples of systems and strategies that improve project results include pre-job planning meetings, weekly job cost production scorecards, tool and equipment checklists, regular training sessions, pre-installation inspection reports, and detailed subcontracts with inclusions and exclusions clearly identified.
Why Systems?
Written, implemented, trained, monitored, tracked, and enforced systems often seem like a lot of work. But they will improve the odds of success. When you let each foreman decide how to install materials based on their own experience, you risk the fact that your installations will not all be performed the same way, and at the same speed. Some will require more labor and materials while other methods will require less. How can you make sure the end result will be correct and on budget if you let everyone decide how they install things versus standard companywide systems?
To improve your field and project performance, standardized and utilized systems will reduce your chances of eliminating problems, errors, rework, callbacks, or over-budget completion. The following is a proven system to improve your project performance.
Construction Project Success System
- Pre-Construction Planning System
a. Contract:
- Read, understand, and follow the executed contract.
- Develop a contract requirement, documentation, and notice chart.
b. Hold Turn-Over Pre-Construction Hand-Off Meeting:
- Attendees should be the General Manager, Sales, Estimator, Project Manager (PM), General Superintendent (GS), Superintendent (S), and Foreman (F).
- Prior to meeting the PM, S and F visit the jobsite to review the plans, develop a construction work plan, draft a preliminary schedule, and estimate the crew hour budget.
- Review scope, inclusions, exclusions, and contract terms.
- Set project goals including budget and crew production goals.
- Establish project schedules, deadlines, and milestones.
- Review proposed subcontractors and suppliers.
- Draft project mobilization, staging, and phasing plan.
- Create project timecards, cost codes, and change order rates.
c. Hold Customer Pre-Job Start-Up Meeting Onsite:
- Train your customers to follow the contract.
- Review contract terms, documentation, payment procedures, approvals, deadlines, milestones, and change order rates.
2. Project Management System
a. Procurement:
- Award, order, and execute all subcontracts and major materials within two to three weeks of job start.
- Confirm all material deliveries four weeks and two weeks before required.
- Deliver all materials to the jobsite a minimum of one week before required.
b. Schedule:
- Develop, confirm, commit, track, and communicate the project schedule to customers, subcontractors, and suppliers.
- Clearly identify and document completion, phase, deadlines, and move-in dates.
- Provide regular updates as schedule changes.
c. Project Management:
- Be proactive and communicate with S and F daily, and with customers weekly.
- PM visits jobs weekly to perform detailed job-walk with S and F to review:
o Contract conformance, quality workmanship, punch list, and safety.
o Job cost scorecard and updated budget including crew labor and equipment production hours and updated job cost scorecard report - budget vs. actual.
o Look-ahead and project schedule.
d. Submittals and Shop Drawings:
- Create a list of required submittals within the first week of job start.
- Include requirements and deadlines in all subcontracts and purchase orders.
- Review and obtain all submittal approvals within three to four weeks of job start.
e. Project Payment Requests & Paperwork:
- Maintain and document all approvals, change orders, requests for information, notices, claims, approved plans, and specifications weekly.
- Prepare and submit project payment requests on time with all required paperwork.
f. Change Order Management:
- Get change order rates approved at customer pre-job start-up meeting.
- Document and manage all project issues, change orders, notices, delays, time extensions, etc. in advance or within two days of occurrence.
- Manage and keep change order requests current - price and submit within seven days.
- Perform no extra or free work without prior written approval.
g. Job Cost Updates, Timecards and Invoices:
- PM approves all timecards daily and invoices weekly with correct cost codes after review with S or F for accuracy.
- PM prepares updated job cost reports and calculates accurate estimated costs to complete monthly. Review with the manager.
h. Project Meetings:
- Hold customer pre-job start-up meeting onsite within two weeks of start.
- Hold customer meetings onsite weekly.
- Hold all subcontractor job start-up meetings onsite.
- Hold weekly jobsite meetings with all subcontractors required on the job within the next 30 days.
- Hold crew meetings including daily crew huddles, crew weekly job reviews, and crew weekly safety meetings.
3. Field and Crew Production Performance System
a. Pre-Mobilization Jobsite Review:
- Before mobilization, GS, PM, or S meet with customers to review site access, staging area, storage area, security, workspace requirements, trash, safety, temporary power, water, restrooms, parking, job rules, move-ins, phases, etc.
- GS, PM, or S visit the jobsite two to four days prior to all move-ins to verify job is ready.
b. Supervision - Pro-active project supervisors provide and perform:
- Daily written job reports with photos.
- Approve and turn in all crew timecards coded to accurate cost codes and work quantities completed daily.
- Turn in company equipment and rental equipment sheets weekly.
- S or F prepare weekly quality, clean-up, and punch-list inspection reports. All identified items are to be completed weekly.
- Weekly safety job-walk inspection report.
- Contact customers, subcontractors, and suppliers three weeks before they’re needed on the job.
- Hold job-walk with GS, S, F, and the customer prior to moving off the job at each phase and get agreement on any outstanding items.
- Prepare the final punch list two weeks before completion and complete all outstanding items before the final job-walk with the customer.
- S and F never leave jobsite without a lead or foreman in charge. S and F never go to the hardware store or supply house - send a crew member if required.
- Enforce company standards, policies, rules, attire, and safety with crew and subcontractors.
c. Look-Ahead Schedule:
- S or F prepare a two- to four-week look-ahead schedule weekly and submit it to the PM on Friday.
- PM, GS, S, and F meet weekly onsite to review the look-ahead schedule.
- Look-ahead schedule to include crew labor, subcontractors, materials, supplies, tools, equipment, inspections, and milestones
d. Overtime:
- No overtime allowed without prior authorized approval and within the estimated budget allowed.
e. Change Order and Extra Work:
- No change order, extra work, or free work allowed without prior authorized approval.
4. Job Cost Scorecard Crew Production Tracking System
a. Accounting to produce weekly updated project crew production scorecards with actual crew hours versus budgeted hours.
b. PM reviews job cost labor and equipment production scorecards weekly with GS, S, and F to develop a plan to complete projects on budget.
c. Hold bi-weekly all S and F meetings to review all project scorecards, production performance results, and areas for improvement.
5. Close-Out and Completion System
a. S or F hold job-walk with the customer before leaving the jobsite at each phase.
b. PM, S, or F hold final job-walk with the customer and subcontractors prior to completion.
c. Estimator and PM review final job cost versus estimate and update cost history library.
To produce optimum results on your construction projects, you must have a system that guarantees performance 95% of the time. Review the factors outlined above and decide which of them will improve your project results. After determining your project performance system, use your list as a template to develop your winning playbook and detailed job descriptions for your team.