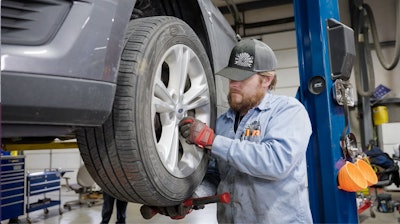
It’s no secret that fleet costs have been on the rise over the past several years, with inflation, emissions regulations, and supply chain issues playing a prominent role in those increases. In a 2024 fleet benchmarking report, data showed the median rental and leasing sector’s cost per mile was $0.60 — the third highest among 12 industries — though fuel spend and distance traveled in this sector were among the lowest.
Because fuel and maintenance are the two highest cost centers for fleets, and because the rental and leasing sector’s fuel spend is on the lower side, the sector’s higher cost per mile could be attributed to maintenance and repair spend. “The National Private Truck Council’s (NPTC) Benchmarking Survey Report 2024, which was released on Aug. 22, found that among private fleets, overall equipment and maintenance costs per mile increased 76 percent since 2020,” according to Penske.
Though the new administration is already making moves to help slow inflation and reduce the cost of doing business, the results aren’t the sort that happen overnight. Early to mid 2025 costs will likely change little, but toward the latter half of the year, we could start to see some downward movement in various business and fleet costs.
Benchmarking Tips & Benefits
While it’s hard to plan for all budgetary challenges that might come your way, you can more easily allocate funds where they’re needed most — or where you see the greatest fluctuation in spend — through benchmarking. Rental fleets can also use benchmarking to assess maintenance effectiveness, compare their performance against industry standards, and make strategic operational improvements.
1. Identify Where You’re At
Before making any big changes, it’s important to first establish a baseline for the metrics you’re tracking — or going to track. These can be things like preventive maintenance (PM) compliance rates, inspection completion rates and failed inspection item trends, service expenses, downtime, cost per mile, and so on. All this data works together to create a clearer picture of the fleet’s health and performance, as well as the cost versus value of assets so you can determine optimal replacement windows.
2. Determine and Prioritize Goals
Benchmarking allows you to compare your operation to the industry standard, like those outlined in benchmarking reports, or you can benchmark against yourself to measure the success of any changes you make. Before you make any changes, though, you’ll want to define specific goals based on the results of your baseline, such as:
- Reducing unscheduled downtime
- Improving service workflows
- Optimizing inventory
- Graduating from reactive to proactive — and even predictive — maintenance practices
Regardless what your goals are, defining them is only the first step. From there, prioritize your goals to help ensure that improvement efforts are focused, measurable, and manageable. In short, don’t start by biting off more than you can chew.
3. Develop an Action Plan
Alright, you’ve got your baseline, and your goals are defined and prioritized; now it’s time for an action plan. Let’s say your priority goal is to reduce unscheduled downtime. You’ll need to first find the cause or causes of the problem, which can include things like:
- Pencil-whipping inspections (or poor inspection completion rates)
- Poor PM compliance
- Harsh driving
- Recurring mechanical issues
- Shop-related downtime due to understaffing, high workloads, or replacement parts delays
Targeting these issues one at a time can help you implement subtle but effective process changes that you can build on over time without getting overwhelmed by either data or change management. You can use digital fleet solutions like a fleet optimization platform to corral all your fleet data in one place to easily see trends in metrics related to your priority goal. You can use digital inspections with set requirements that include photos, documents, or comments to reduce pencil-whipping and improve inspection compliance rates, for instance. Likewise, digital work orders with estimated versus actual time to repair and status updates can shed light on where shop delays might be occurring.
4. Measure and Adjust
This is the point where benchmarking against your baseline really comes into play by enabling you to track your progress over time. Measuring key performance indicators (KPIs), such as cost per mile, downtime rates, and the impact of maintenance process changes on overall fleet efficiency allows you to see what adjustments have worked, what hasn’t, and what still needs a bit of fine tuning. Adjustments should be made as needed based on real-time data, but don’t be afraid to scrap a change that’s had a negative impact. It’s also important to set expectations after changing a process to allow a sort of buffer zone between implementation and payoff so stakeholders aren’t expecting a 15 percent cost reduction in one day.
Remote Maintenance Management
The key to benchmarking is data, and not just any data, but useful data. Many fleets are already using fleet management tools for data collection, including telematics and fleet maintenance software. Some fleets are even opting for a fleet optimization platform to consolidate fleet, finance, and business data through integrations. Pairing telematics with an optimization platform enables easier remote maintenance management; you can track and monitor asset issues and assess the severity of those issues no matter where vehicles or equipment may be.
Using fleet solutions doesn’t just make benchmarking easier, it provides a level of data visibility and automation that can improve maintenance workflows. All the data mentioned above — and more — is accessible in real-time and displayed visually on a customizable dashboard so you can focus on the metrics most important to meeting the fleet’s goals.
Digital inspections provide failed item alerts from which you can create an issue and attach it to an existing or new work order. You can receive DTC fault alerts in real time and take a snapshot of related sensor data, which can also be attached to existing or new work orders, speeding up issue diagnosis. You can include priority statuses on digital work orders to ensure the most critical issues are addressed in a timely manner. You can also use fleet solutions to optimize your inventory based on usage trends and set re-order thresholds; parts assigned to work orders are automatically removed from your inventory in the system.
Using fleet solutions as a benchmarking tool to help guide maintenance decisions can help rental fleets reduce costs and downtime and stay competitive within the industry. And, with automation features and robust reporting, optimizing your operation becomes a more manageable task.