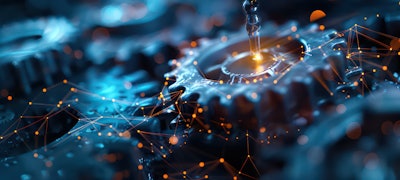
Imagine two different construction fleets, working identical projects in the same region. In one, each piece of equipment uses its own lubricant, specifically chosen to maximize that machine’s performance. In the other, one product has been selected that functionally lubricates the entire fleet. This fleet trades total optimization for a simple and efficient maintenance process with minimal risk of human error and easy substitutions in the case of a sudden shortage or contamination. Which approach is better?
If you’re experienced in the construction sector, you know the answer is “it depends”—on the scale of the project, on the number of machines being used, and even on the climate your fleet operates in. Once you factor in all these variables and complications, it becomes clear that choosing the right single lubricant or library of lubricants and the right team of professionals to support that choice with routine changes or analysis is vital to achieving your goals and providing stand-out service.
Why Your Entire Fleet Relies on Your Lubricant Decisions
Everything that happens on your work site is affected by the decisions you make about lubrication, making it almost impossible to overstate its significance. The biggest reason to devote resources to a comprehensive and tactically sound lubrication strategy is simple risk mitigation. Using a suboptimal oil impacts a machine’s performance and, in many cases, can shorten its lifespan or even cause permanent damage. Whether it’s burning oil or the wrong grade was selected, that decision will result in unplanned downtime, negatively impacting efficiency and causing delays.
A poorly planned maintenance program can also have a negative impact on your bottom line by eating up more time than it needs to, wasting resources, failing to prevent downtime due to equipment failure. It’s a delicate needle to thread: changing oil too frequently is a waste of money and negatively impacts your uptime, while more widely spaced intervals risks loss of efficiency or even, in some cases, permanent damage to equipment.
A further complication is that adjusting a maintenance plan in the middle of a project is difficult. For example, if you change the type of oil a machine uses after three months on the job, that will create inconsistent performance and confusing data that can hamper your ability to assess drain intervals or read the results of an oil analysis.
These changes in performance could have a trickle-down effect on the rest of your fleet, and spikes in wear metals or additives could create misleading analysis results. Experts will agree that consistency is key to a successful lubrication plan, but maintaining consistency when you don’t have a clear vision for what products you want to use and how you want to support them can be challenging.
Finally, factor in the risk of human error, which occurs with even the most professional teams. Every time you add a new product to your supply and every decision that further complicates your lubrication strategy, increases the risk that the wrong oil will be used in the wrong machine or that the lubricant will become contaminated. These simple errors can result in a loss of efficiency, unplanned downtime or even total equipment failure.
Devoting Time to Your Lubricant Plan Pays Off Down the Road—Big Time
The solution is a comprehensive lubrication plan developed and supported by experienced experts who can factor the following into the choice of lubricant and grease supply:
- The length and scale of the project
- The type of machinery being used
- Regional climate
Once the project is underway, that team can support those choices with a regular oil analysis program.
Regular oil analysis can be more effective than routine oil changes. Instead of regularly changing out lubricant and replacing it with fresh product at preset intervals based on past machine performance and original equipment manufacturer (OEM) recommendations, oil analysis involves regularly sampling oil and delivering the samples to a laboratory for analysis. The results are comparable to a blood test performed by a physician. Experts examine the lubricant sample for:
- Wear metals, indicating excess wear on the machine
- Contaminants, indicating a leak or issues with lubricant storage
- Signs of early degradation, indicating that the machines are working harder than anticipated and the lubricant is having trouble maintaining the necessary viscosity
This data can then be used to adjust worksite strategies like switching lubricants, moderating how the machinery is used or any other number of tweaks.
The lubrication engineers who perform the analysis work closely with OEMs, maintaining up-to-date information so they can correctly interpret the results and determine what (if any) problems a piece of equipment might have. They can also determine if the machine will need its next oil change earlier than expected or, in many cases, later than expected. Armed with this data, fleet managers can appropriately plan for downtime with more foresight or take advantage of the extra efficiency to reduce cost and waste and even get ahead of schedule.
Lubricant Data Can Be One of Your Most Useful Tools
A meticulous lubrication plan supported by routine oil analysis has even greater benefits at scale. As the construction industry expands into more diverse fleets powered by a mixture of power sources like battery electric and hydrogen the benefits of these strategies will become even more pronounced. Access to detailed data about your fleet can result in greater efficiency, allowing you to meet or exceed sustainability goals while decreasing costs without delaying or compromising results.
Experts can also recommend specific greases and other supporting products that will work ideally with the best lubricants. They can also help fleet managers decide how many specific lubricants to use for their fleet, balancing the advantages of optimizing machine performance and efficiency with the possibility of contamination or human error resulting in the wrong lubricant being administered to the wrong machine.
When performed correctly, this proactive, rather than reactive, approach will provide:
- Longer machine life
- More efficient production
- Earlier prediction of incoming challenges
- Smoother, faster, better performance for your entire team
Once establish a plan, lubricant data becomes one of the most important tools in your fleet. It provides unparalleled insight into the performance of your equipment and arms you with the knowledge necessary to provide exceptional results.