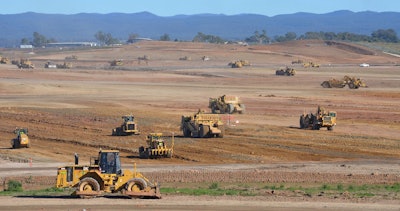
It has been said that great dozer operators are never hired based on their ability to fill out paperwork, timecards, maintenance reports, progress updates or budget forecasts. These represent the information chain contractors require to compile accurate bids; maintain construction schedules; and ultimately, satisfy customers. With data flowing from all directions inside and outside the jobsite, having a more connected, reliable way to manage and communicate data is critical for a successful and profitable project.
As Michael Tilson Thomas, artistic director Laureate of the New World Symphony, puts it, “A major part of what a conductor does is get a large group of people to agree on where ‘now’ actually is.”
Do you know where “now” is on your jobsite? If not, you may be prime for a more connected jobsite. Four construction industry technology pros to discuss what requirements must be met to achieve a fully connected, well-functioning jobsite.
What Is a Connected Jobsite?
A connected jobsite tracks all the materials, equipment, tools and talent on a jobsite, sharing the data in real-time with personnel and systems in the field and office to measure a project’s progress against the master plan. This usually involves equipment hardware, such as sensors, cameras, and telematics, communicating with construction-specific software and systems via Wi-Fi, cellular networks, or GPS capabilities.
The idea is to streamline the acquisition, communication, and processing of jobsite data—with minimal paperwork or delay—so that timely decisions can be made that positively affect the profitability and quality of work in progress.
A connected jobsite can be large or small, from 20,000-acre airport sites to compact office parking lots. Contractors outfitted with full capabilities can track multiple projects across a region, gaining a single source of truth across the enterprise from one central control hub. A connected jobsite can be large or small, from 20,000-acre airport sites to compact office parking lots.Trimble
“There may be hundreds of pieces equipment, idle or in play, ranging from loaders and trench diggers to smaller tools, like buckets and jackhammers, spread over miles of territory at one time,” said Larry Baker, CEO FleetWatcher. “There’s no way to keep track of it all without some sort of digitally connected system,” he said. “If you can’t see it, you can’t track it. And if you can’t track it, you can’t improve your operation. It’s that simple.”
What Are the Telltale Signs of a Non-Connected Jobsite?
Non-connected jobsites are generally managed manually, by walking the site, carrying hard copies of plans and updates, and discussing progress with machine operators directly or over cell phones. Data is gathered after the fact and usually involves “guesstimates” of data such as hours worked, materials moved and fuel burned. These historical records usually lead to miscalculations, errors, and time and materials wasted, along with expensive rework to correct mistakes after the fact.
According to Chris Richardson, senior director of industry workflow for Trimble Civil Construction, the difference between jobsite connectivity and non-connectivity comes down to “sneaker-net.” That is, “someone wearing boots (sneakers) running all over the place to distribute updates and check progress—not a very good way to run a business.”
Gage Witt, senior product consultant for Caterpillar, echoes the sentiment. “You may be seeing good, steady or even growing productivity, but the profit doesn’t match. That’s a sign that your jobsite is out of sync.”
Other signs include:
- Excessive fuel consumption when machines run idle
- Persistent cost and schedule overruns
- Design changes that take days to filter into the field
- Unexpected equipment maintenance
- “Stale” jobsite information
- Time sheets based on the “honor” system
- Lost equipment
The experts agreed that data is the most important driver of a connected jobsite.Trimble
What Technologies Are Required for Full Connectivity?
The experts agreed that data is the most important driver of a connected jobsite. For this reason, equipping a jobsite to manage data effectively is critical. Data collection hardware, supported by back-end software that makes sense of that data, forms a sound technology foundation. However, nothing of value can be achieved without linking the data collectors with the data receivers, and that points to the Internet. With this in mind, let’s survey the basics.
Hardware generally refers to the devices that collect data at your point of attack. Hardware includes Internet of Things (sensors) and telematics devices that automatically report the usage, whereabouts and operating condition of the tools and equipment in the field. They may display information on your machines’ screens, on a laptop positioned in a jobsite trailer or in the corporate office. They provide the physical feeds your team needs to monitor the site, share plans and communicate effectively as work progresses.
Software enables the jobsite. It reads the inputs that your hardware collects and helps your team members make sense of the information collected. Construction-specific software may allow you to modify design models on the fly, survey equipment conditions, monitor costs in real-time, update schedules, even assemble bids based on past field calculations.
A good software package will help you analyze trends, build forecasts and manage tasks. When integrated with back-end systems, managing inventory, procurement, and finance operations becomes easier, payroll becomes simplified, and compliance with safety and operational standards can be assured.
Of course, none of this is possible unless the hardware and software work together. Cloud systems are ideal for this kind of collaboration. They provide:
- Browser-based access to information over any device
- Support massive computing power to crunch numbers in near real-time
- Facilitate application integration, either through open-source technology or common application programming interfaces
“The internet is the pipeline that makes the connection possible,” said Richardson. “That’s always the first piece to consider in a digitally connected world.”
From there, connectivity options expand. Mike Kucharski, vice president of sales & marketing for Gauge Telematics, lists several options for a GPS-connected jobsite, including wide-area cellular networks; local area Wi-Fi connectivity; satellite communications for remote area access and near-field communications; or Bluetooth connectivity, for low-cost, short-range connections.
“GPS technology simplifies the integration of such core jobsite elements as [manufacturer] data, on- and off-road GPS devices, ERP systems and other fundamental equipment management technologies,” Kucharski said. His company represents an enterprise asset and fleet management platform that tracks and manages equipment-intensive operations with telematics and other tools. “The goal is to create a single source of truth, from the corporate office to field supervisors; machine operators; maintenance techs; suppliers; and other stakeholders, including customers.”
Full connectivity relies on assembling the right hardware, software and virtual connections necessary to collect, store, assess and analyze the data you need to run a successful operation.
Where Is the Best Place to Start?
“If you’re not already operating connected jobsites, a good place to start would be to try a simple locater to track where an asset is,” said Witt. “Connecting your fleet is easier than you may think. The first time you recover [a] lost asset, avoid downtime due to some major maintenance project or realize a fuel savings at the end of a quarter, you’ll see you’ve more than paid for the initial investment. It’s all about [the] return on investment.”
Some hardware and software components are offered on a subscription basis. This can be an excellent way to test a system short-term. Pick a manageable jobsite and outfit it for connectivity. At the end of the test, determine how you came out and where you can improve and expand your base from there.
Many contractors manage jobsites across a wide region, where as 300 to 400 machines may be out in the field. It’s not unusual for one to be stolen. Having an asset tagged can help the contractor recover it.Trimble
Many contractors manage jobsites across a wide region, where as 300 to 400 machines may be out in the field. It’s not unusual for one to be stolen.
“Once a machine is tagged, the data is available 24/7,” said Witt. “We helped a customer recover a stolen machine within a day of its [going] missing. Had it not been tagged, that could have been a $50,000 loss.”
Kucharski developed an equipment management maturity curve delineating tactical/traditional activities, such as tracking equipment hour and location information on the low end, up to advanced fleet monitoring of large equipment in remote areas, such as mining and quarry operations, at the strategic/world-class end of the spectrum.
Figure 1. Equipment management maturity curve.Gauge Telematics
What Are the Benefits of a Connected Jobsite?
“I’d say [the benefits begin] the moment you start working with a digital design model,” Richardson said. “Having your design information in a digital format immediately sets you up for instant sharing of updates, which immediately reduces errors and rework and improves the accuracy and quality of the finished product.”
Kucharski stated that “connectivity is the backbone for moving up the maturity chart, where significant operational efficiencies start to unfold.”
Detailed information becomes the norm, aiding in productivity planning, operator consistency and workforce improvement. Costs come down and profitability goes up, matching any gains in productivity. All equipment can be accounted for, including maintenance status and fuel us, adding to efficiency and equipment lifetime value.
Back-office functions also run smoother, eliminating information blind spots and delays associated with traditional paperwork and fact-gathering. Bids, budgets and schedules become more accurate, supporting sales efforts while building the brand. And above all, customer satisfaction increases, enhancing loyalty and expanding word-of-mouth advertising.
What Advice Would You Give Someone Regarding Connected Jobsites?
Take some time to assemble your brain trust and evaluate your processes. Where are the bottlenecks? Where are the leaks? What is it you want to improve?
“If you are honest, you will find an opportunity to improve performance on every jobsite,” said Witt. “By identifying what you value most, you will be able to determine the hardware, software, subscriptions that will benefit your operation most and compress the time it takes to get there.”
Talk to several suppliers and schedule a few demonstrations. Read their contracts and make an informed decision. If you need to hire a consultant to guide you in the process, find one but own the decision.
And don’t forget, people will always be involved. “Within the grand scheme of things, you can monitor equipment, but what you really need to do is to get all your people on board,” said Baker. “You can only improve what you measure, and if they understand what matters most, they will be more likely to get on board and drive the train into the station.”
Over Time, Millions Can Be Made
The benefits of a connected jobsite far outweigh the risk or expense. Understanding what’s happening “now” on your jobsite can compress project turnaround times, improve productivity and create a huge competitive advantage for your company.
“In an information war, the one who knows first is the one who performs best,” said Richardson.
In a short period of time, connecting your machines to your people and your people to what’s happening in the field can lead to decisions that contribute millions to your bottom line. So, why wait? Connect your jobsite for enhanced operational efficiency and improve your project throughput—“now.”