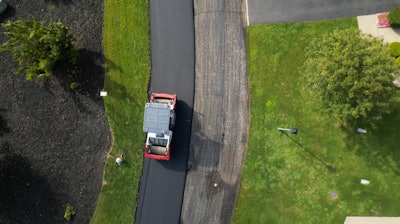
It's an age old question: Is bigger better? For rollers and meeting your compaction needs, the answer to this question is as nuanced as it is in every other instance. Rollers come in all kinds of sizes and specifications, as well as, with all kinds of various new technology these days. To find out if bigger is better, you first have to ask yourself what types of circumstances and jobsites you need a new roller for.
For the last few years Royal Pavement Solutions (Islip, NY) mostly focused on doing work in the commercial market space, including large parking lots for big box stores and some smaller residential road work when possible. This season they faced their largest road project to-date working for a home owners association.
One of their biggest challenges would be how quickly they could complete the work, as the HOA wanted to minimize the disruption to the residents daily comings and goings. The neighborhood has only one entrance way, and long stretches of the loop-road that winds through all the houses would be inaccessible. However, the Royal Pavement Solutions team had a brand-new ace up their sleeve in order to ensure an efficient process as possible.
While attending World of Asphalt 2024 in Nashville, TN, Kenny Roy, the owner/operator of Royal Pavement Solutions (RPS), was definitely looking to add a new roller to his arsenal. After seeing what the show had to offer, he landed on the Dynapac CC2200 VI equipped with the SEISMIC on asphalt technology.
With a max operational weight of nearly ten tons and five feet of compaction width, it's by far the biggest roller that RPS has at their disposal. It joins their two other Dynapac models, the CC950 and the CC1200, and they regularly bring all three to the jobsite and deployed them effectively in different ways.
Who's The Boss?
The project at Sunken Ponds Estates was greater than 113,000 sq. ft., and included 3" depth of milling (1313 Cu. Yd.) and repaving (2100 tons). It would require full traffic control, minimal disruptions to residents, and no interruption of trash or delivery services. On top of that, due to the age of the community, emergency services access would also have to be maintained.
The goal? Complete everything in less than three days. RPS was more than up to the challenge. Day one they would mill and prep the surfaces, cleaning everything up and getting ready for paving on day two. Day three would be for traffic markings, and the HOA club house parking lot.
Now, being a member of an HOA usually comes with some minor concessions to be apart of the community group. It's not unusual for some members to be a little particular, and, sometimes, that behavior can continue when it comes to contractors trying to get their work done.
"When you come into like a private HOA like this, you might have one person as a point of contact, right?" said Kenny Roy, standing next to their brand new roller. "What can be a problem sometimes is that residents have places to be, friends to visit, kids to get to school and back, beach day, or whatever. They're all bosses then. But we've been doing work in this community for a couple of years, and these people have been really great. We haven't had anything negative at all."
When Less Is More
One of the big advantages of a smart system for your roller like SEISMIC is that it can prevent over-compaction. When you over-compact your soil, base, binder, or wear layer past a certain point you're weakening the overall integrity of the material. That means premature cracking and other breakdowns in quality or strength. Additionally, you end up wasting a lot of fuel, add unnecessary wear-and-tear hours on your machine, and, you're wasting time that could be spent finishing the job more efficiently.
There are different tech platforms out there that can help prevent over-compaction and help you track your compaction data, for example: BOMAG's BOMAP, Caterpillars Intelligent Compaction, HAMM's Smart Doc, and other add-on third party pieces of tech that sometimes require GNSS receivers. There are several options for you to be able to track and measure density, temperature, and number of passes.
What's so different about the SEISMIC technology built into the CC2200 VI is that it takes those readings directly, and then every .2 seconds it is assessing any adjustments that should be made to the intensity and frequency of the drum vibration.
"What's really nice about this machine, why it's different, is that you get kind of used to the vibration turning on-and-off automatically. It's signaling to you that the area is ready or not, and you can move on," explained Hector Polanco, operations manager at RPS. He's spent the most time using the new roller since it was delivered.
"If I feel the frequency kick up really high, I know it might take another pass, because obviously it's less compacted and the system is picking that up," said Polanco. "When it goes down, then I'm already figuring out the next area hit. Everyone has there own way of doing things, and I've got a pattern I normally follow, but this makes a huge difference."
Hector's Compaction Pattern:
Step 1: Starting from the edge, no vibration. While backing up, turn vibration on.
Step 2: 50/50. Align the drum halfway over from the edge of the first pass, putting your water line in the center of the drum.
Step 3: Once you reach a seam, if it's still really hot and freshly paved, could continue 50/50. However, if it's already started to cool down, then he works over more gradually using 25/75, or only a quarter of the drum on the uncompacted side. Rinse and repeat.
When More Is More
Could RPS have completed this project using their two smaller Dynapac rollers? Of course they could. However, their ability to meet the timeline that the client asked of them would have been severely impaired.
"Let's say we were paving today without the big roller," said Roy. "At the speed we are laying asphalt today, in order to get this done, the smaller machines would absolutely not be able to keep up with our pace. It's not just the SEISMIC stuff either. To have five feet of compaction width, going back-and-forth way fewer times, Hector can keep up with us really easily."
While the smaller rollers in their lineup followed further behind, finish rolling and working out any potential marks left in the initial passes, with each new truck, the CC2200 and Hector were ready and waiting to go.
"It makes a real different when you go to bid on a job," said Roy. "It's changed the game for us in terms of how much we can do and how fast we can get it done."