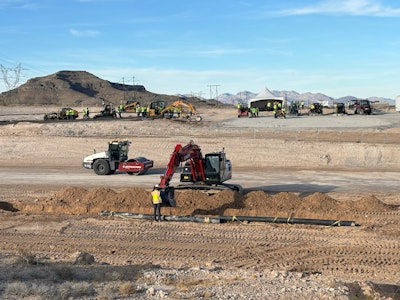
Trimble Dimensions 2024, held Nov. 11-13, 2024, in Las Vegas, Nevada, is an annual conference organized by software, hardware and services company Trimble, bringing together professionals across the geospatial, construction, agriculture and transportation industries. The three-day event featured keynote presentations, hands-on training, networking opportunities and exhibits showcasing the latest innovations and solutions in construction technology and software. This year’s installment also featured a sizeable off-site setup for equipment operation and technology in the field.
With a record-breaking 7,000 attendees and more than 800 educational sessions, the event is aimed at supporting industry professionals’ desire to better understand the future, especially with regard to technology applications in the real world of construction.
The 2024 theme, “New, Next, Now,” focused on the company’s vision for the future, including expanding connected capabilities, technology integrations, new collaborations and partnerships, and a wealth of cutting-edge technologies, all pointed toward its goal of solving problems in the construction industry.
Alongside a busy schedule of events and future-facing technology releases throughout the event, Trimble made several major announcements, including news about the extension of its longstanding joint venture (JV) with Caterpillar, the introduction of Trimble’s Siteworks Machine Guidance Module for compact track loaders, and more.
Trimble & Caterpillar JV
The Trimble/Caterpillar JV expansion is aimed at enhancing interoperability, innovation and adoption in construction technology. According to Trimble executives, key drivers include growth, market acceleration and technology advancements. The partnership, which is now in its fourth iteration, focuses on integration across different systems and workflows, enabling customers to use products across various infrastructure. Trimble notes, “Innovations like the chassis-mount system and automated excavation have improved efficiency and accuracy. The new agreement also includes a distribution model to extend Trimble’s technology reach and a 3D grade-ready factory option for Caterpillar machines, offering flexibility in activation and ownership. The goal is to support both skilled and non-skilled operators, with a focus on future-proofing technology and maintaining customer preferences.”
Siteworks Machine Guidance Module for Compact Track Loaders
Trimble announced Siteworks Machine Guidance is now available on compact track loader buckets. The news, which marks the first new machine type for the Siteworks Machine Guidance Module since it was introduced for excavators in 2023, is Trimble’s first machine guidance solution designed for compact track loader buckets, providing one solution for layout, grading and leveling. Users can move the system among multiple machines and jobsites, and also employ their existing technology on-machine easily by adding a machine kit and the Siteworks software module. Trimble shared, “The Siteworks Machine Guidance system includes the Trimble SPS986 or Trimble R780 GNSS Smart Antenna with tilt compensation and the Trimble ProPoint positioning engine, and any bring-your-own-device or Trimble field tablet that supports the Siteworks software. The module enables contractors to use Siteworks off the machine to design, measure and lay out projects. Contractors can then transfer the GNSS receiver and field tablet from the pole to the compact track loader or excavator to provide in-cab, 3D machine guidance and grade checking capabilities without the need for a surveyor.”
Autonomy and AI
Throughout the week, Trimble executives encouraged discussion about the future of autonomy and AI, offering fresh outlooks and insights.
“Our institutional view on autonomy is: it’s a series of progressive automation,” said Trimble President CEO Rob Painter. “We’re not institutional believers that we’re going to wake up one day and have Level 5 autonomy — machine control guidance is emerging at Level 1 and Level 2,” he said. Painter pointed out that the company, which has been developing IoT, autonomy and AI solutions for decades, recognizes that not every task on a jobsite is fit to be completed autonomously, noting that many of its latest autonomous innovations are currently in beta testing with customers. The technology, which is not yet available to the market, is one step in a longer journey to find which construction challenges are best suited to be solved with autonomy.
Trimble is now testing an autonomous excavator and compactor, both of which were in action at the off-site location throughout the event (pictured above). Painter says the company is essentially working backward to pinpoint customer problems and opportunities for automation, and working to drive efficiency, which in turn becomes the path toward autonomy. For instance, another potential opportunity might be in linear trenching applications.
Ian Welch, director of engineering, autonomous solutions at Trimble, says the bigger focus is on how to get more machine control onto more machine types and bring more types of assistive technologies to operators.
“How do we take [these] learnings and technologies and spin them into actual products we can use today?” said Welch. “One example is steering control for autonomy. We put steering control in compactors as a product called Autosteer — it’s also in earthmoving equipment, bulldozers and dozers. The idea is to better utilize that equipment to get a higher return, both with more accuracy and more efficiency,” said Welch, who notes the ultimate aim is to provide solutions that help contractors run their businesses better.
“[Going] back to the compactor example: It’s a pretty basic machine, but how do you do exactly what you need to do, no more, no less? We’re working on software that allows you to plan exactly where that machine should go to give you perfect overlap,” said Welch. The same is true for road construction applications, where rolling out dirt or asphalt, minimizing overlap and optimizing precision are critical to project success.
Geoffrey Kirk, product manager, autonomy and assist at Trimble, notes that Trimble today is investing in solutions to help make its products better for autonomy tomorrow.
“We are on a journey to autonomy,” said Kirk, “[We are] taking what we learn from making a machine fully autonomous, such as [an] excavator, and we’re leveraging that information and those learnings to make assistive products available sooner.”
Kirk points out that developing fully autonomous machines means fully understanding what a particular workflow might demand.
“We want to help you run your site better, interacting with the equipment, the geospatial model, the design, so we can optimize what you’re doing — that’s a key part for us,” said Kirk.
According to Kirk, adding more machines and learning from autonomous flows within a mixed fleet is also important. He says today, Trimble supports compactors and excavators, but over time, it will add more machines to the autonomous marketplace.
Optimization is key, according to Kirk, who is finding that operators want the quality improvements and the production improvements that come with fully automated systems, however, they’re often not quite ready for the idea of full autonomy.
“We will be bringing out these assistive systems in whatever place a customer wants, and at whatever level of autonomy they’re ready for ... to bring those improvements in productivity out into those markets sooner.”
Before the market is able to realize a fully autonomous future, Welch says there are a few priorities earmarked for Trimble along the way. “We look at autonomy as a test bed, first to learn and try new things, then to develop those technologies into products,” said Welch.
“So the journey to get there will be more automation, more automation, more automation, and, eventually, we’ll get to a point where we will have automated all these tasks, and the maturity of the perception system software will have graduated to a point. Then, we’ll come together and be ready for a fully autonomous [future].” For now, he says, the approach is, “How do we provide value to people sitting in the machine to do their job today?”
The Warthog robot is being tested to autonomously move around, stop, scan and provide progress updates and data to field operations.IRONMARKETS
Autonomy and Adoption
On the subject of technology adoption, Welch notes there are typically two camps. “One camp is: We’re all in, we love it. And the other is: I can do it better than the machine can,” said Welch. “In order to win people over, you have to show them.”
The autonomous compactor, while seemingly basic, is one such example of proving value in the technology. Welch says being able to provide performance data — hitting on efficiency and precision — the idea becomes a more of a reality to some of the technology or autonomy holdouts. “If the [autonomous] compactor does it 10% or 20% faster than an operator, they can start to see [the possibilities],” said Welch.
Autonomy, while important, is not the company’s only focus. “AI is big to Trimble right now,” says Welch. “How can we make even small improvements? If I get a 5% to 10% improvement by using AI, that’s real money that people care about,” Welch said, which ultimately creates more investment and interest in it.
Alongside common concerns about safety, Welch says the No. 1 challenge for autonomous adoption comes down to an issue of trust. “How do I know it’s doing the right thing?” Much like today’s robot vacuums, end users may wonder whether the device is on the right path to accomplish the task it set out to complete.
“It takes a day or two to realize you don’t actually care how it did it, because you didn’t have to do it,” said Welch. “That will be the big quantum leap on some of these things. It might not be how you would do it, but did it do the job efficiently?”
On the safety side of site operations, Welch says end users will encounter the same curiosity: How do we know that’s where we need the machine to be? Welch notes that regulatory representatives have proven through engineering controls and practices that the technology is, in fact, safe, however, doubt may still linger. “If we can take some of this technology and slowly introduce it to contractors and operators, over time, they will naturally get more comfortable with it, so, with time, they can begin to trust it.”
A Look at the Future
According to Painter, a fully autonomous world is possible, but that point is further down the road. “I think it’ll be further than what prognosticators will tell us,” he said. “That autonomous side of autonomous equipment needs a brain. What work are you going to do? How are the machines all coordinating? When are you going to refuel? When are you going to recharge? You need a work plan. All the things [Trimble is] doing, we see them as the brain.”
When it comes to the future of autonomy, Welch says we are on our way. “I always look at automotive leading indicator,” said Welch. “[The prediction has] always been ‘five years.’ And the next year, it’s ‘five more years,’ the next year, so on.” said Welch. “I think we will see simple machines, like either asphalt rollers or compactors, be automated first,” which he says could take place potentially within the next 10 years.
“We can show value today, but the big leap [for potential end users] is going from ‘person in the cab’ to ‘no person in the cab,’ because we have all these sensors, perception sensors, cameras, LiDAR, radars, etc., and they work well, but they have to be guaranteed to work in a functionally safe manner.” And as industry regulations and standards develop around autonomous technologies, all parties are aiming to keep up and figure out how that might unfold.
Although it doesn’t appear that the jobsite will be filled with empty cabs tomorrow, there is a genuine concern that such technology will keep operators out of a job. However, Welch says the opposite is true. Right now, autonomous technology needs skilled operators’ expertise to learn from.
“We’re not going to punch some keys on a keyboard and figure it out in 10 minutes. There is a journey we need to take to get there,” said Welch. “How can we partner with operators and what is the best way to do this operation? Or why do you do it this way? Or what can you teach us about this? We actually want to work with [operators] to figure out how to do it. It’ll be a long time before anything replaces field operators,” said Welch.
According to Welch, one of the most exciting parts of being on the path to automation is the optimization of tasks on the jobsite. “Yes, we have autonomy, and, yes, we will get [to a fully autonomous future] eventually, but what can we accomplish along the way? And I think that is optimizing the things people do every day,” said Welch. “It seems pretty simple, but if technology can make you 2%, 3%, 5% better, that’s a real improvement.”