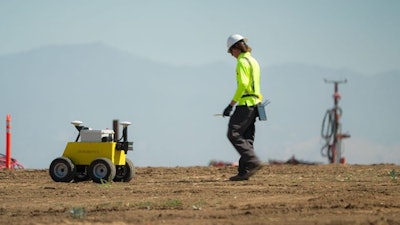
Global navigation satellite systems (GNSS) have transformed numerous precision-oriented industries over the past few decades. Construction, in particular, has greatly benefited from the real-time positioning data in satellite constellations like GPS, GLONASS, Galileo, and Beidou, enabling a more seamless, speedy, and accurate realization of engineers’ plans in the real world.
Most construction firms now rely on GNSS signals for conducting everything from initial site surveys to live progress check-ins for their projects. Yet, atmospheric interference, technological discrepancies, and more can distort the accuracy of GNSS signals, throwing off results by several meters.
In construction, 10 centimeters could be the difference between smooth project execution and catastrophic problems. Ultimately, firms need GNSS positioning that gives accurate location to within a few centimeters, no matter where they work.
Precision Demands in the Construction Industry
It’s impossible to understand the importance of signal correction without first considering how integral GNSS technology has become to construction work. In particular, firms rely on GNSS signals in four critical areas.
Site Survey
Surveying has always been a foundational aspect of construction planning. Mapping and staking the construction site is essential in preparing to break ground and build on site. Surveyors begin the task of bringing engineering plans from vision to reality.
This work may take place from the air and/or on the ground, and it now typically involves a vast array of tools to ensure accuracy, including drones, cameras, lasers, sensors and GNSS signals. The data from GNSS is invaluable in helping surveyors and engineers create digital twins, virtual representations of the physical site that they can update in real time to ensure the work in progress matches the plan on paper.
Robotics
Robotics have further transformed the work of construction, in terms of both site surveying and building. Rovers, drones, and construction robots can execute various tasks to improve project efficiency and reduce costs.
Once again, GNSS signals play a critical role in ensuring robots carry out their tasks effectively and accurately. Land surveying rovers, for instance, rely on real-time satellite data to navigate construction sites and mark spots for construction with pinpoint precision.
Damage Prevention
Construction work is highly invasive, penetrating the ground where hidden power, gas, and water lines lie. Misfires during this process can have substantial cost implications or threaten the safety of construction crews.
Construction firms can use GNSS signals and other complex instruments to prepare for safe excavation. These tools provide detailed location information for underground pipes and wires and ensure contractors don’t damage critical underground infrastructure and cause costly delays or dangerous work conditions.
Engineers can also use GPS data to pinpoint where future utility lines will be, ensuring construction doesn’t get in the way of laying pipelines to bring the constructed building online.
Site Inspection
GNSS data continues to be instrumental while construction work takes place. As builders lay foundations, frame buildings and add finishes, engineers and inspectors can collect site reports and use satellite data to update digital twins and verify the work is on track.
With updated and accurate digital twins, planners have a real-time view of the work in progress, which they can use to inform plans, budgets and timelines as the project unfolds.
Limitations of GNSS Technology
As important as GNSS technology is in construction work, standalone GNSS measurements are not as precise as they need to be for these applications. GNSS data is typically accurate to within 1–2 meters. In harsh conditions, it may even be off by more than 10 meters.
GNSS has several inherent error sources that contribute to inaccuracy. Variability in atmospheric and ionospheric weather, as well as satellite clock and position errors can cause position calculations to be outside the bounds needed for construction.
To make matters worse, it’s often difficult to tell when GNSS signals are off the mark. And when errors do appear, they’re often persistent, requiring a way to address and correct them on a more systemic level.
Ultimately, construction work isn’t technically impossible without GNSS corrections, but it’s much more time- and labor-intensive, and less accurate overall.
RTK positioning relies on a network of base stations in communication with satellite constellations to achieve cm-level accuracy.Point One Navigation
Finding True Precision in Construction
In the past, correcting these errors required companies to install site-specific base stations, which could cost upward of $50,000 each, plus labor; a necessary but painful expense. Now, construction firms have access to more modern, efficient, and affordable options:
- Real-time kinematics (RTK) Networks: RTK requires a base station, which can be set up to transmit signals with rovers in the surrounding area. Using the distance between the base station and rovers to verify location data, RTK can deliver accuracy to within centimeters. RTK networks consist of collections of base stations that provide coverage over broad geographic areas.
- State space representation (SSR): This newest form of GNSS correction technology offers the most expansive analysis of factors that impact signal accuracy, but it usually requires specific vendor support or even a conversion of service.
- Precise point positioning (PPP): An accurate correctional option, PPP relies on a collection of precise stations to assess potential errors and refine the data. However, the PPP network is too limited to allow for quick signal correction — it can take 20 minutes or longer for signals to converge. This makes it a poor fit for construction use cases that require real time accuracy - including surveying, drone inspection, or robotics.
For time- and precision-sensitive applications like land surveying or underground inspection, RTK is the most efficient way to provide the highest level of accuracy. But there’s one important caveat: RTK is only as good as the network providing the correction.
Legacy RTK networks require pre-jobsite planning and on-the-job setup. For each specific location, a crew must connect to a different base station. Yes, continuously operating reference stations (CORS) are open to the public for local georeferencing, but they are state-specific and vary widely in terms of reliability and performance. It’s common that construction crews do all of the prep work, arrive on site and their local base station isn’t working, resulting in labor waste.
Achieving RTK corrections without significant overhead requires construction companies to work with an RTK partner that designs its products with these challenges in mind. For the most effective results, the provider must offer an extensive network of base stations, reliable connectivity, and built-in capability of converting measurements into various local datums.
When these standards are met, RTK delivers superior, cost-effective corrections accurate to within a few centimeters or less, radically improving construction project planning and execution.
Civ Robotics builds rovers for construction surveying.Civ Robotics
RTK in Action
What does this look like in modern surveying applications? Consider a few examples that rely on advanced RTK corrections.
Civ Robotics builds rovers for construction surveying. Precision is paramount in surveying, and Civ Robotics uses Point One’s extensive Polaris network of RTK base stations and correction devices, complete with local-datum capabilities, to achieve centimeter-level accuracy for massive solar farm installations and other projects. Assisted by Polaris, its rover operators can mark coordinates six times faster than traditional surveyors.
In another essential construction application, the company Radiodetection uses ground-penetrating radar products to avoid damaging critical utility infrastructure during ground-breaking. RTK helps Radiodetection achieve survey-grade precision to avert catastrophic accidents and project delays.
In both cases, achieving sufficient precision would be impossible (or highly cumbersome) with GNSS signals alone — or even with a less reliable RTK network. With access to a broad network of RTK devices and built-in local datums, firms like Civ Robotics and Radiodetection capture the centimeter-level accuracy construction demands — without the time or cost of other options.
Few elements are more important to construction than precision, and the industry has long relied on GNSS signals from GPS and other satellite constellations to ensure buildouts match their designs. But GNSS alone isn’t enough for true survey-grade precision, making correction essential for GNSS applications in the field.
While firms have several choices for correcting GNSS signals, RTK sets the standard for cost-efficient precision. With a broad enough network of base stations and easy conversion across regional boundaries, RTK provides reliable, cm-accurate measurements, virtually every time. In an industry always at risk of overbudgets or costly delays, that level of assurance is priceless.