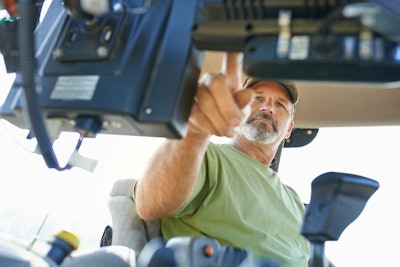
Whether it’s vehicles that are used in agricultural environments, or on construction sites, all off-highway vehicles have one thing in common – they operate in extremely challenging conditions. Because of this, their systems and components must be designed to withstand long duty cycles in the presence of humidity, moisture, dust, dirt, and constant vibration. Without such robust engineering, both productivity and safety would be at risk.
As if those environmental challenges weren’t difficult enough, operational limitations exacerbated the problem. Machines being guided by sight, using mirrors and cameras, had to deal with blind spots could put personnel in harm’s way or cause operators to run over obstacles. And without insight into the health of the machinery, workers sometimes continued to operate systems that needed maintenance, adding to safety risks while also increasing the likelihood of a major mechanical failure that would put the vehicle out of commission.
Fast forward to today, and thankfully, advanced technology has made many of these challenges a thing of the past. Original equipment manufacturers (OEMs) now use sensors, connectivity, telematics software, and artificial intelligence (AI) to create new functionality, solving common operating challenges and increasing safety and productivity for owners and operators of off-highway vehicles.
Sensors at Work in the Construction Industry
Throughout a construction site, sensors are virtually everywhere, and their job is critically important. Construction vehicles use sensors, including humidity, temperature, pressure, rain, fluid, and oil quality detection, to monitor external operating conditions and internal system performance. These sensors help ensure reliable performance of mission-critical operations where downtime is not an option. Sensor-enabled construction vehicles include a mix of electrified equipment and legacy internal combustion engine-operated systems. Electrified equipment is used heavily for closed-loop applications, that have predictable operating conditions and easy access to charging.
In fact, as electrification becomes more mainstream, sensors can make this a more viable option for a wider range of off-highway applications. Rotor reposition sensors attached to motors track their rotation and provide signals so that electronic control units can optimize output and battery pull, extending battery range.
When combined with high-speed data connectivity, sensors power advanced driving-assisted systems (ADAS) such as e-braking and e-steering. Operators driving to job sites can use these systems to minimize turns, lights, and delays, speeding arrival while minimizing fuel costs. They can also leverage pedal travel sensors, which convert foot pressure into signals to brake to stop slowly or suddenly. High-pressure brake sensors detect how fast wheels turn, providing the right amount of pressure for calipers to break smoothly, lightly, or heavily while avoiding locking up.
Finally, sensors can detect problems before they occur, enabling operators to conduct proactive maintenance in the field, offsetting costly repairs and returning vehicles swiftly to service. As just one example, a multinational company uses oil property monitoring sensors to protect costly off-highway vehicle engines from harm and reduce repair timeframes from six days to two.
Connectivity Systems Coupled With Artificial Intelligence
To increase productivity and maximize efficiency of a jobsite, connectivity systems must be robust enough to support real-time data capture and transmission, ingesting data on how the surrounding environment is changing, including nearby vehicles.
In today’s environment, many construction vehicles already leverage some degree of automation to drive throughput and increase worker safety on the job. Both manually operated and autonomous vehicles use sensor-guided systems to make tight turns in constrained spaces, turn in unison to avoid collision, and avoid rolling over.
What’s more, GPS systems with LIDAR and RADAR sensors integrate with telematics software to provide the real-time location of all machinery, while proximity and other sensors detect blind spots and the proximity of nearby equipment.
Couple these systems with artificial intelligence (AI) and we’re on our way to an even safer, more productive jobsite. AI is becoming increasingly integrated into various aspects of the construction industry, but not without the power of sensors behind it.
Let’s take for instance the idea of wanting to create a 360-degree view of a jobsite. To achieve this, sensor data captured around the site is aggregated and combined with artificial intelligence to create a real-time picture of the environment’s current and changing conditions, such as the movement of personnel, machinery, and materials.
Sensor-driven systems with AI increase safety by detecting hazardous conditions on sites that could harm humans, such as opportunities for slips and falls, and hazardous materials aren’t being used safely, such as chemicals. When systems detect these issues, operators then receive alerts to address hazards immediately. Supervisors can also be alerted if there is an accident on the jobsite that requires attention.
From a preventative maintenance standpoint, AI algorithms analyze sensor data to predict when maintenance is needed, offsetting costly downtime, and potentially preventing on-site accidents before they even happen.
And as we look to the future, we can expect to see AI-powered robots and automated machinery performing repetitive tasks on the jobsite, such as digging trenches, moving earth, or building brick walls with great precision. Not only does this increase productivity, but also improves safety by limiting hazardous tasks, and creates new and expanded job opportunities for workers. Autonomous vehicles can also take over jobs that are too dangerous for personnel, such as tearing down large structures.
Ultimately, the goals of owners in the construction industry have largely remained the same. They not only hope to optimize the routing of trucks that bring materials and personnel to job sites, but also seek to drive the reliability and productivity of heavy machinery to keep projects on schedule while at the same time ensuring operator and equipment safety.
However, as the pace of innovation accelerates, the need for close collaboration among ecosystem partners will increase to meet these goals. By working closely with OEMs, component manufacturers will be able to meet the ever-changing needs of the construction industry by embracing the advancements in AI and working to develop even more advanced sensors that improve productivity, reliability, and safety, bringing new solutions from concept to market.