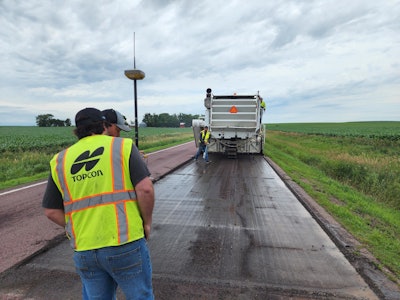
What’s one everyday necessity almost everyone takes for granted? Smooth roads and highway systems. “You never notice when you’re driving on a well-maintained road, but you’ll be sure to notice when it’s not,” said Cody Wagner, roadbuilding technologies product manager at RDO Equipment Co.
Uneven slopes, potholes or deteriorated asphalt increase wear and tear on your vehicle, and you’ll be in for a noisy ride. In recent years, many, including the federal government, have recognized the need to invest in restoring roads because of their age, heavy use from increased traffic volume, inadequate maintenance over time and the impact of weather conditions.
As I’ve transitioned to lead RDO Equipment Co.’s Wirtgen Group business across 12 states, I’ve connected with original equipment manufacturers (OEMs), pavers and roadbuilders as they partner to gear up for what may be the busiest year yet. And according to many, these roadbuilding projects are long overdue.
American roadbuilders began building our interstate highway system in the 1950s. Back then, they couldn’t have known that drivers would enjoy the quality of these roads for more than 70 years. In fact, the Texas Department of Transportation (DOT) reports that its oldest highway, the Gulf Freeway, I-45, first opened in 1951. The road is slated for an extended lifespan, too, as late last year, the Texas DOT celebrated the groundbreaking of the I-45 infrastructure project, designed to expand roadway capacity, reduce congestion, improve safety and enhance mobility. These “mega infrastructure” projects, like the I-45 in Texas, are made possible by the Infrastructure Investment and Jobs Act (IIJA), community support and technological advancements in roadbuilding equipment.
As we look forward to the first half of the year, we are cautiously optimistic that these IIJA funds will continue to trickle down to meet the demand to revitalize our roads and highways. While we can’t predict the forthcoming actions of a new administration, we can pave the way to the future by following roadbuilding fundamentals to improve something that many of us rely on every day.
Smoother Roads Are Safer Roads
Most drivers don’t notice when pavers achieve accurate compaction for optimal smoothness, but when ride quality deteriorates, it is sure to be a topic of conversation at the diner.
“Ride quality is how comfortable riding down the road is,” Wagner said. “It’s about the surface being even, without unnecessary bumps or ruts.”
Uneven roads cause more friction and impact on both vehicles and the road itself, leading to the need for more repairs and all the time, money, materials and emissions associated with doing the work again. Wagner explains that smoother roads reduce vehicle wear and tear and are safer, too.
“When a roadway has unintended varying slopes, a driver is more at risk during certain weather conditions like ice or fog,” Wagner said. “When roadbuilders focus on improving ride quality during every pavement pass, they ensure we all can arrive quickly and safely at our destination.”
GPS and Telematics Data Keep Track
With the ability to connect machines to fleet management software such as John Deere Operations Center, roadbuilders can track specific data points, like GPS location or production hours, to share withdirect stakeholders.
Wagner, who has worked for more than eight years in paving quality control partnering with state and county municipalities, explains that these entities will highlight areas that require attention.
“After the state, county or city selects certain roadways for repair, they will determine if it’s a complete rebuild or resurfacing project,” Wagner explains. “Roadbuilders use GPS equipment, like Topcon positioning systems, to mark these areas.”
Before any asphalt removal, resurfacing or paving begins, the contractor and subcontractor will analyze the GPS-marked areas and determine the intended depths based on the current roadway’s changing slopes. Then, the roadbuilding team will use the data they’ve collected from surveying to develop a digital model with their milling operators.
“Once the team has a digital plan, they’ll spray paint to mark intended slopes and depths,” Wagner said. “After milling, the team will survey the road to determine if they need to do a leveling pass to fill in spots before paving to ensure optimal compaction.”
RDO Telematics Support Manager Larry Herman Jr. explains that tracking a paver’s location optimizes the roadbuilding site when many stakeholders require real-time info, like the length and depth of paved passes.
Roadbuilders use surveying equipment like Topcon Positioning systems to record varying slopes quickly.RDO Equipment
A Good Road Starts with a Good Base
Ultimately, any roadbuilding team will monitor the paver’s grade closely, continuously monitoring thickness to achieve the road’s appropriate density for its environment.
The roadbuilding team determines the road’s density based on the soil and weather conditions of their community.
To achieve the density, roadbuilders compact the soil, aggregate or asphalt to remove air voids. “Optimal compaction while paving is the base of any smooth roadway,” Wagner said.
Wagner explains that without proper compaction, roads will be more susceptible to cracking and other forms of distress.
“Proper compaction cannot be achieved when the paving mix reduces in temperature due to environmental factors like air or ground temperatures,” Wagner said.
“When the mix loses heat, and its temperature cools, the mix will be ‘hard to stick,’ become brittle and will not have the structure or binding that occurs from compacting at an accurate temp.”
To ensure a smoother profile, several roadbuilding teams in states like Minnesota use Topcon’s RD-M1 Scanner. The RD-M1 Scanner is a LIDAR (Light and Detection and Ranging) scanner fitted to the back of the truck. A DOT team member drives the roadway to record imperfections and roughness.
“We then load this data into a mill equipped with 3D milling technology and software, using GPS and LPS (local positioning system) to guide the mill,” Wagner said.
“After milling, we use these same data points, plus the grade information from the scan, so the paving team will have the machine data and control info to pave a smoother profile.”
Machine Monitoring and Control Prevent Problems
Paving and milling crews are among the earliest adopters of roadbuilding technology.
Crews used strings to guide machines in building straight roads, but since the integration of telematics, OEMs have developed machine control technology. Wirtgen’s AutoPilot system eliminates the need for strings and uses satellite navigation. With the AutoPilot system, roadbuilders can pave complex geometric shapes like curves.
Most roadbuilding crews use an autopilot system so project managers can program depths for operators. Often, a foreman and project manager will review data points automatically collected at the end of the day to check if the paver has completed the planned path. Roadbuilders who partner with telematics experts and connected support teams can learn best practices for making data-informed decisions.
“We can track whether machines are working or idle, which helps fleet managers allocate resources. We can also monitor fuel usage, machine speed and engine data,” Herman Jr. said. “We can focus on the entire job site to partner with a roadbuilder to effectively manage projects and to plan for future roadbuilding bids.”
As we gear up for the next phase of infrastructure development, roadbuilders can follow the same fundamentals that roadbuilders established nearly a century ago.
Since the IIJA passed in 2021, government funds have covered planning costs to assess various roadbuilding projects’ scopes.
In the coming months, we should expect roadbuilders to have the necessary info and funds to procure the latest equipment or technological solutions. With this information, roadbuilders can partner with a trusted dealer to precisely pave smooth roads to last for decades.