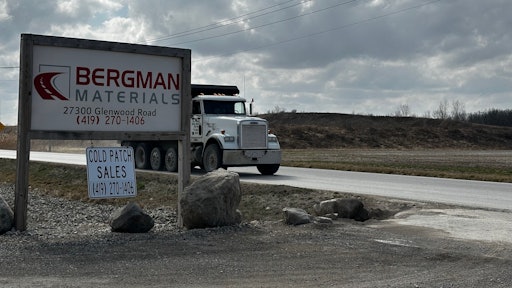
In the state of Ohio, there are a few large companies that carve up a majority of the Department of Transportation road projects every year. From talking to contractors from other states, this is not too uncommon. The state DOTs have a handful of companies that they are familiar with, have good track
Every asphalt-pavement contractor is either a small-to-medium sized operation, doing commercial paving work, buying asphalt from the larger companies that make up the other half of the state's industry. This can make it difficult to continue to grow if you're a commercial pavement professional who wants to break into DOT, municipal, or other types of larger scale local work. The challenge gets pretty sticky for a number of reasons.
If the large-scale companies who dominate the market, your competitors, are also the places you have to go to buy your asphalt, then it's definitely going to limit your ability to grow. It means you're always going to be paying more for your asphalt than the companies buying it from themselves, and it also means that you're going to have to wait in line, because their day-to-day projects are going to take priority over yours.
However, there are still some contractors out there finding a way to be a growing mid-size asphalt, paving, and road work company despite these types of market conditions. They're doing it by buying their own asphalt plant, one that produces enough mix for themselves to start, and has room to grow in the future to sell to others like they were previously doing.
Who Would Take This On?
Henry W. Bergman Inc., and the Bergman family's history in the area concerning road building goes back far enough to predate modern techniques.
"Great grandpa started in 1912. He did roadwork, commercial, blacktop, and culvert work in the winter," said Paul Bergman, vice president of the company. The Bergman family literally built up the Genoa area. "I think we actually laid lumber down to start route to a sectional."
Lumber isn't the type of base we would use today, but Bergman's paving division has been involved with every facet of the asphalt industry. Paul got his start shaking striping paint cans in a Taco Bell parking lot when he was seven years old, but the company has done crack sealing, sealcoat, and anything in-between. If it has to do with asphalt, they've been there.
Where they've really grown there business over the last decade or so has been getting involved with DOT work as well as rural road repair with a form of chip seal and paving.
"Anytime they mill out a street -- it's called an inner layer," explained Bergman. "We'll do a chip seal and then pave on top of it. That helps with reflective cracking so it doesn't come up through as fast. It's kind of like a glue interlining layer."
Getting Into The Production Side
At a certain point it was clear that if they wanted to continue to grow, and deliver at the pace and quality they wanted, a plant might be the best option. After considering several manufacturers, they decided to go with Asphalt Drum Mixers (ADM) EX 8844.
Around 2019, just prior to the COVID-19 pandemic, the company began to finalize the details, and then in early first quarter of 2020, they set the plans in motion. Footers were laid around February, and then the unthinkable happened when a huge portion of the country shutdown in an unprecedented way. Work and health restrictions at the time made the construction a challenge, but they forged ahead as best they could.
After a short delay, they placed a call to ADM that the site was ready, and trucks started arriving. A little more than a week later, they had their plant, although it didn't come online fully until later that year in July of 2020.
Location, Location, Location
Interestingly, while this is the only plant that Bergman has, this wasn't the first time in the company's long history that it was producing asphalt in the area.
"In the early 50s. My grandpa decided to build a plant in Oak Harbor," Bergman told me, and showed me a picture of an old half-ton batch plant that still hangs on the walls of their offices. The plant operated with them for six to eight years before it was sold off. It's not completely clear what happened, but Paul has a hunch it had to do with the logistics of the time.
"My first thing is logistics, right," Bergman said. "You have to be near projects to pave them out of the plant. Back then you didn't have big dump trucks, yet. Just single single axle trucks, and possibly some horse and buggy still." Unfortunately, Oak Harbor wasn't the most ideal location for an asphalt plant at that time. This generation of Bergman wanted to ensure they didn't repeat history, and make the same error. The selection of a good location for a new plant is essential.
"We found our quarry in Perrysburg (OH), it's near Toledo and the surrounding area. Logistically, for us, it was a good move. To be able to control your schedule more, as well as the pricing on the material."
Going to School
Every new step of growth has its own new challenges that it brings with it, however, and once they overcame a pandemic, shutdowns, delays, and everything else, they had to figure out what to do next.
"Just to be able to read the job mix formulas, and all the testing that goes behind one of those was a learning curve," said Bergman. "You just want to make sure your plant is always producing the same thing. Once you have the right ingredients and how to run these basics tests, making sure it meets the right criteria, you're good to go."
It wasn't without one or two hiccups at the start. Their first few batches came out brown, due to a mixup with the wrong type of sand. However, with each challenge they've faced, they pull-back examine the situation and, sometimes with extra help from ADM, then make the proper adjustments.
This is where I met the namesake of the company Henry W Bergman III, who was out at the plant when we caught up with him. The day I visited the location, he was working through an issue they were having in the drum.
He explained that the aggregates weren't hitting the exact optimal position for their asphalt veil. To help me understand he took out a marker and drew on the side of a metal panel to illustrate the issue. The arrangement and type drum flightings, in this case those that were bucket shaped, was such that it was dropping the material just beyond the center line of the burner.Brandon Noel
When this happens, it can take longer for material to reach the desired temperatures, and result in loss of efficiency. Through trial and error, they'd figured out where the adjustments needed to be made, and were making sure everything was set for the upcoming season a few weeks away.
I asked if there were any regrets or things they'd wished they known at the start, which they would do differently in hindsight. Going ahead with a new plant for the first time, were there any lessons they'd want themselves to know?
"We only wish we'd gone with ADM for the RAP [recycled asphalt pavement] system, too," said Bergman III.
They had bought a used system, and saved some on the costs, but there were some complexities involved with the setup that could have likely been avoided otherwise.
"Getting the insertion exactly right was a bit of a struggle, and I think it might have been better to just go all in on everything."