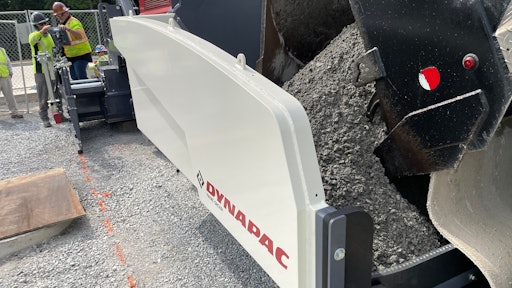
Perhaps, you never thought you'd see the day where concrete was the subject of a feature in Asphalt Contractor magazine, much less putting it on the cover of an issue! However, roller compacted concrete (RCC) is an exciting product and process, growing quickly in popularity among industrial, commercial, and even some residential markets. It's sturdy, versatile, and asphalt paving crews already have ninety percent of the skills to utilize RCC, because it utilizes the toolset, machinery, and much of the knowhow from the asphalt side of the pavement world. Whereas concrete contractors implement slipform pavers, RCC requires asphalt pavers, tandem rollers, and density gauge testing to achieve the required final product spec.
Of course, it isn't as simple as going to the nearest concrete plant, placing an order for whatever they have on hand that day, and dumping it into your asphalt paver. I don't want to undersell the nuance and complexity of RCC, because using it requires all the characteristics and technicality of an experienced asphalt paver. But I do want to make the case to you that, comparatively, it appears to me to make more sense for traditional asphalt contractors to take an interest in RCC and add it to their offerings. There's more crossover here than you might expect, and there's even ways to bring asphalt in and combine them.Provided by the RCC Pavement Council
Also, it's important to note that RCC is not an asphalt replacement, or even an alternative, because it's biggest opportunities are mostly for jobs that asphalt isn't well suited to. It isn't a solution for long stretches of highway with fast moving, heavy traffic. Learning about RCC and potentially adding it to your wheelhouse is about broadening your market potential into whole new areas.
What is RCC, and why should you know about it?
It's origins lie in Canada in the 1970s, and it was initially utilized in the same situations it is predominantly used in today: large industrial areas with lots of traffic, but where that traffic was slow moving or mostly static. The pavements met their needs well, as they were low-cost and quit resilient in standing up to extreme loads and the specialized equipment used by loggers. It would be an understatement, however, to say that the technique didn't exactly catch on in a big way or set the world on fire.
"The whole proposition behind RCC is that it's incredibly durable for big intermodal facilities with extremely high static loads," said David Zuehlke, who works in the role as Dealer Sales Manager, South-Central, for Dynapac North America.
Provided by RCC Pavement Council
To put it into perspective, from 1975 to 2010, there were only 172 documented projects. Then there was a massive period of growth in the number of applications starting in 2011. In just four years (2011-2015) there were 369 projects, which more than doubled the number of projects performed during the previous thirty-five years. Similarly, the next four year span grew that number to 453 RCC projects, and this trend is expected to continue.1
Historically, industrial and commercial jobs have dominated the bulk of RCC jobs. Ports, large distribution centers for retail and big-box stores, and some commercial work. In 2021, however, roadways became the leading sector, more than doubling in demand year-over-year. A Large portion of that growth was driven by contractors in the asphalt industry discovering RCC and getting into the field with it. It's growth periods have also been somewhat tied to periods where oil prices were particularly volatile.1
"You can think of it as a blend of asphalt, concrete, and soil technology," said Corey Zollinger, chairman of the RCC Pavement Council. "It is really a blend of those three and understanding that as a contractor is the key to being successful at it." This blending of technology is similar to Zollinger's background, because he received his Masters in asphalt, while his dad was a professor that taught concrete. This gives him a unique perspective on the two worlds that collide to make RCC a reality.
"From the asphalt contractors perspective, we're using all their same equipment," Zollinger continued. "The asphalt paver and the the rollers are the same, the basic skill sets behind using those machines are essentially the same." The entire paving train should look familiar to any asphalt crew. Dump trucks carrying the mix, backed up to the asphalt paver, with large tandem vibratory rollers initially behind the screed, and smaller finishing rollers behind them. The density is even measured using the same types of gauges.
How do asphalt pavers achieve this, and how can rollers ride on top of concrete that's just been laid down without sinking into the surface?
Not Your Typical Mix Design
The type of concrete you see coming out of the large spinning barrel trucks is worlds apart from RCC. What separates the traditional type of concrete from RCC, is that it is a much drier, aggregate dense material, more akin to what you would see with asphalt. In the concrete world, the amount of moisture, and therefore its liquidity, is referred to as a mixes' slump. The higher the slump, the more flow to its state.
"Moisture content is definitely the biggest difference," said Brodie Hutchins, Vice President, Head of Sales, Vögele Products. "It's the difference between pouring concrete and placing concrete. Slip form paving will oftentimes refer to pour and it's more of a liquid versus zero-slump, which is really dry.The consistency is very similar to asphalt. It has fines to keep the aggregates together.”"Negative" slump concreteProvided by RCC Pavement Council
Zolllinger describes its slump value as even less than zero. "I call it a negative slump concrete," he said. "I say that because if it even comes close to flowing, you got a problem. It kind of has the consistency of wet gravel."
Typical mixes use a fifty-fifty ratio of sand and aggregate, and preferably a washed river sand instead of manufactured types. No rebar or other reinforcement is used either. One of the benefits of this dry mix design, is that it can open to pedestrian and light traffic in just twenty-four hours, as well as to commercial traffic in forty-eight hours. Who can produce this type of mix design? Can you call up your nearest concrete plant and have them flip the switch? The answer is, it's slightly more specialized.
"We recommend it be done mixed with a twin shaft pugmill," said Zollinger. "however, it has been done with wet batch plants on other types for smaller projects, we don’t recommend ready-mix trucks except for trial batches."
This brings up a very important detail concerning the paving of RCC. Up until this point, we've highlighted the crossover it has with the asphalt industry. However, just like there is a preferable plant type to produce the mix, there's also a specialized type of asphalt paver that is logistically the only choice for those serious about exploring RCC as a new product they can offer their clients.
High Density Paving
In 2023, we covered the differences between the types of asphalt screeds that are primarily used in the U.S. market versus the screeds typically used in Europe. As it turned out, the tamper bar and pressure bar, high compaction screeds that Europe uses have a small but growing share of the work here domestically. That is likely due, in no small part, to the burgeoning demand for RCC; because it requires:
- a high level of initial compaction off the screed,
- a low amount of roll-down, and
- a desired finished density greater than 98 percent.
High density pavers, like those that have variations of tamper-bars and/or pressure bars, in addition to vibratory screeds, are essential to achieving the necessary goals for RCC paving. In fact, it's possible that in the early decades following the invention of RCC, its usage and popularity stalled due to the use of commercial pavers that couldn't achieve the proper level of density off the screed. Contractors gave it a shot, tried it out on their pavers, experienced integrity failures, and decided it wasn't viable. However, the problem was simply that they weren't using the proper instruments.Provided by Wirtgen Group
"The finished density is absolutely key," Zuehlke emphasized. "For every 1 percent of air voids left in RCC you're losing 5 percent of your strength. For example: if you only achieve 95 percent compaction, you will only have 75 percent of your original intended design strength."
"First, you must understand the application, because, just like asphalt, each job is a little different," said Hutchins. "Before we get to the equipment, it is more of a consultative thing, to understand: how wide, how deep, what's the mix, and what's the timeframe? Because in a high-density screed, the tamper stroke goes up and down based on the thickness of the mat. It's a lot like amplitude on a roller. If a contractor is placing eight inches of RCC, we'll make sure that that screed tamper is set for a higher stroke adjustment and we adjust the pressure bars which are located behind the screed plate. You've got to have more force to push down eight inches versus pushing down two inches. Other than that, the lay down process is exactly the same.”
The most important piece is that the screed contains two or more compacting devices of some kind. Most highway contractors laying down a two-inch overlay typically are not using compacting devices. Although they probably incorporate vibration, the real final smoothness is coming from the rollers. That isn't a feasible approach at six or eight inches of RCC placed in one lift, without some kind of compaction element within the screed. It wouldn't achieve proper rideability.
The good news is that a high density style paver isn't so specialized that it will collect dust when you're not doing RCC jobs. It's still excellent at producing high quality asphalt mat and there are no changeovers needed. One day it can run RCC and asphalt the next. And there's some indication that the winds of the industry itself might shift in the future to favor the high density screeds, thus, such an investment would be ahead of any coming curve.
"I don't know that we're not at an inflection point," said Dynapac's Zuehlke. "The way the market is going, with initiatives to lower stack temperatures at the asphalt plant, I think it might create some changes. We may look to higher density pavers to do things like they do in Europe. Case-in-point, a contractor chasing after airport work, bought a high density paver, the same paver that we're doing RCC with. He could lay cement treated base with it, and handle the really stiff asphalt mix designs that airport's require, and he could pave wider."
It can't be overlooked, or overstated, that despite all the overlap there are still a lot of technical hurdles to overcome for those contractors who want to enter into RCC. As is the case with incorporating any new technology, machine, or application, training is key.
Practice....We're Talking About Practice
One thing is for certain. You don't want to invest in a high density paver, source a good quality RCC mix design, and then show up on a large jobsite for the first time thinking that your asphalt crew can get 'er done, transferring their asphalt expertise one-to-one. It doesn't work that way.
"What I normally tell contractors to do, is to pave in their own backyard. There is a bit of a learning curve with it," said Zollinger, warning that attempting to learn on-the-job can be very costly. "Do test sections in your backyard with with a consultant, someone who knows how to handle the materials, how to do the mix designs, and find areas where you can just just pave. Get some experience putting the material down, and then find a project that's as square as possible. Large parking lots or stretches of roadways are a good starter."(Left) Dynapac's SD 2550 CS dual tamping foot paver. (Right) Vögel's Super 2100Provided by Dynapac NA
Currently, the market options for high density pavers in the United States is a fairly thin playing field. The two biggest players are primarily, but not exclusively, Vögele, and Dynapac. Although, in the past, Volvo also had a model capable of doing RCC with the ABG7820C they were only produced from 2005-2015.3 For Dynapac it's the SD 2550 CS dual tamping foot paver. Vögele offers two models, the Super 2100 and Super 3000, with the 2100 being their more popular model with the AB 600 TP2 screed. Both Dynapac and Vögele's screeds are capable of achieving post-paver densities in the mid-nineties under the operation of a trained crew.
Why Not Both? The Benefits of RCC
When it comes to selecting a pavement material, asphalt is still king. That is especially the case when considering ride quality, smoothness, road noise (especially at highway speeds), flexibility, texture, and the ease and speed with which it can be repaired or replaced. We should all understand, however, that road building shouldn't be an either/or conversation. It should be about what product works best for a given scenario:
- What's most cost effective for the client?
- What will best suit their needs?
- What's the most sustainable and environmentally conscious design?
- What material will be more resilient for a given climate region?
Given that ideal criteria, RCC has some legitimate credentials to consider. Firstly, RCC is extremely durable, as we've already established in looking at its primary historic use cases. It can take a beating, and that's why places like the Port of Houston decided to use it. But it can play an even more direct role in a city's infrastructural selection, especially in places like Houston that have borne witness to extreme meteorological catastrophe in recent history.
Provided by the RCC Pavement Council
More and more climate events like these do significant damage to roads by washing out the base, and destabilizing the soil. RCC fares better in these settings due to its monolithic structure.2
Compared to conventional concrete solutions, RCC is put down much faster (up to 48 hours for commercial traffic), costs about 15% less, and produces between 10-15% less emissions.
It's also more versatile than traditional concrete surfaces. After it's paved, the appearance is more akin to that of asphalt, although a grayish color rather than black. It can also be treated through various methods to give it different surfaces finishes. For example: you can give it a diamond grind finish, use power trowels to achieve a broom finish, and, perhaps most importantly, it can be capped with an asphalt cap. This option literally delivers on some of the best of both worlds.
"RCC is a really just a structurally sound base," said Vögele's Hutchins. "There's hardly any curing time, so you're able to get back on the mat or get traffic opened up right away. If you put an asphalt cap on these zero-slump mixes for applications such as a freeway then you're going to get all the benefits of asphalt, as well."
You can find more detailed information and resources at the RCC Pavement Council at http://rccpavementcouncil.org/