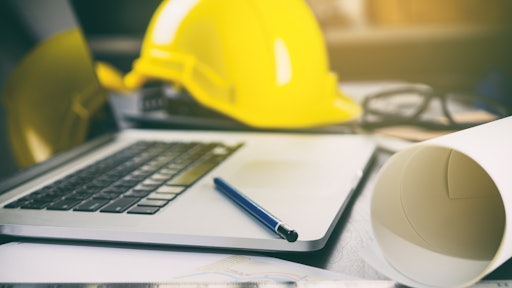
At the first PAVE/X Conference in San Antonio this past February, I must have hit a real nerve for many contractors and field leaders. When asking leaders if they had a challenge with workers making mistakes that needed to be reworked or that caused a “go back,” the response ranged from smiling, nodding their heads in agreement, or just displaying frustration. To make matters even more realistic, I then shared what the “cost of quality” is for mistakes that are made.
The “Godfather of Quality,” Dr. Edward Deming, found that when a mistake is made, the actual cost of correcting the mistake is some three “times” the amount of the cost associated with doing something right the first time. Let me give a brief and simple example.
A paving contractor has a crew that overlays a mat that is ten-thousand square feet, with a cost of $5,000.00. That’s not what we sold the mat for but what the cost of putting the mat in. Now, our crew makes several mistakes requiring the complete removal of the one-to-two-inch mat and then replacing the mat. Here’s what the numbers look like, per Demining:
1st Placement $5,000
2nd Remove/Replace $5,000
3rd Lost Opportunity Cost $5,000
Total Cost $15,000
The third cost always surprises contractors but think about it for a minute. While your crew is reworking a mistaking, they could have been executing another project, for the first time.
Aside from not having enough money to make payroll for the start-up contractor, poor quality can bring any contractor to their financial knees. The Cost of Quality is a real separator of contractor between those who do things right the first time from those who just seem to always have issues causing rework and call-backs. So, what’s a contractor to do? Consider the following brief tips reduce, if not eliminate your quality issues.
- Start taking more focused time on defining exactly what each project will require, including more accurate descriptions of the property the work will be executed.
- Have a focused “pre-start” meeting with the estimator and the crew that will be doing the asphalt, sealcoating, striping, etc. project.
- There should be a written plan for larger or more complicated projects.
- Always provide your crews with the right equipment and tools to execute the job.
- Depending on the complexity of the project, the estimator, senior field leader, or the owner should be visiting the project to ensure that we are completing the work as planned.
The Cost of Quality is zeroed out when we do things right the first time. Spend more time on the front-end of the project, addressing the five tips above, and watch your production, safety, and profitability all improve!
Here’s to NO BAD JOBS!
Brad Humphrey, known as The Contractor’s Best Friend, is President of Pinnacle Development Group. For more information about Brad, his company, or this article, contact Brad at [email protected].